Gear Pumps Solve Viscous-Flow Problems at Industrial Wastewater Treatment Plant
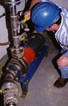
Johnstown Wire Technologies, Inc.
Summary
Gear pumps in the company's water treatment plant handled nearly five million gallons of lumpy liquid polymer over the last five years. Gear pumps, metering difficult methanol for the company's annealing furnaces, turn in similar performance.
Johnstown Wire Technologies, Inc. (JWT) began life as a unit of the huge Johnstown, PA plant of Bethlehem Steel. When the steel plant closed its doors in 1992, the wire mill was purchased as a stand-alone business. It has been flourishing ever since.
As a relatively small cog in the overall steel complex, the wire mill didn't get much attention. As a stand-alone business, with a dedicated and enthusiastic marketing staff and the flexibility to buy steel rod competitively, production is rolling. JWT output has grown from 7,000 to 14,000 ton/mo. The 150 seasoned steel professionals who came along with the mill are now part of a staff of 300.
The Wire Business
JWT's major commitment is to high-quality cold heading wire to supply the fastener industry. Some two-thirds of the mill's production goes to cold heading customers, to be cold-formed into fasteners. Construction staples are a related market.
The firm also makes electrogalvanized wire, aluminized wire and wool wire. In addition to its obvious polishing and cleaning applications, the wool wire (steel wool) is used by the automotive industry to make semi-metallic brake pads, and heat sinks for the explosive charge in automotive airbags. A percentage of JWT production is shipped overseas, mainly to offshore branches of U.S. customers.
Water Treatment: Keeping Pace with the Booming Business
JWT employs an advanced clarifier water treatment system, adding a dry polymer as flocculent. The septic system operates continuously; it is automatically adjusted to match treatment needs, which vary according to water flow, treatment plant operation and solids loading. The polymer requirement can vary from 2.5 to 3.7 gpm.
A flowmeter totalizes polymer usage on a daily basis, including average flow for the whole day, number of liquid polymer batches added and total amount of feed needed.
Rotogear Pump Improves Polymer Pumping Performance
As originally installed, the system employed a progressive cavity pump for the polymer metering service. The pump did not stand up to the service: sheared pins and rotor and stator wear were common occurrences, and seals and packing glands frequently caused maintenance problems.
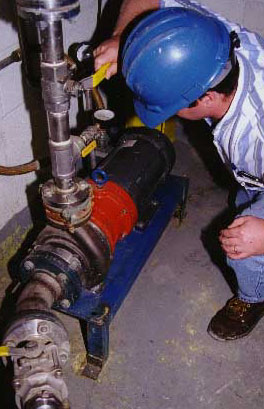
Plant maintenance management, under the direction of controls analyst Mike Cassidy consulted with Glen Teeter of Delta Pump & Systems, Inc., its pump supplier. After extensive investigation, it was decided to install a Liquiflo positive-displacement, rotary gear pump as a better alternative for polymer addition. The pump selected was a 37°F Rotogear, mechanically sealed 3 Series with a maximum capacity of 10 gpm and 1,750 rpm. The investigation also concluded that selection of Teflon bearings and low operating speed, would insure a long life for the pump.
The pump was installed during a routine plant shutdown. In the five years the pump has been on stream, there have been no problems. Maintenance staff simply cleans the suction and discharge lines from time to time when they notice the pump is working harder.
With the dry-mix liquid polymer system, the pump is moving a viscous fluid with occasional lumps of dry polymer. They are handled with no trouble.
Operating Details
The Rotogear pump is operated with a DC controller and no gearbox. When applying a positive displacement pump for metering, flow is varied by changing rotational speed. The gear pump runs at 500 rpm, or below, on 24-hour service.
Nine months after the gear pump was installed, a Fisher-Parker magnetic meter was added to meter pump discharge. Operations management has concluded that the gear pump/meter combination provides "a lot better handle on how to run a treatment plant."
The totalizer now indicates more than four million gallons pumped since the meter was installed. Counting the nine months of operation before the meter was added, the Rotogear pump has handled nearly five million gallons of liquid polymer with no operating difficulties.
Rotogear Pumps for Methanol Metering
Based on the successful service of the polymer pump, similar Liquiflo Rotogear pumps were selected for methanol service on the wire mill's annealing furnaces. The methanol, at a rate of from two to eight gpm, is metered into the furnaces as an agent for controlling atmosphere. Metanol is a thin, low-lubricity product which must be handled at relatively high pressure. It's also volatile, highly flammable and toxic—the chance of leakage is a serious environmental concern.
The pumps originally used on this service had problems with seals and packing. Clearly, sealless magnetic-drive pumps were the way to go: the Liquiflo Rotogear pumps have eliminated environmental concerns of leakage and cleanup. And, while long life is not expected of a pump on methanol service, the Rotogears' silicon-carbide bearings delivered two to 2.5 years of life on 24-hour service before rebuilding was needed.
Additionally, each of two production furnaces is equipped with two Rotogear four-MC pumps, running at 1,200 rpm with T/C shafts. One pump is in use, the other for immediate backup. The maintenance department keeps a fifth pump on the shelf for emergencies, but in 2½ years it has never been called into use.
More information on Liquiflo pumps is available at:
N/A
443 North Ave.
Garwood, NJ 0727
Tel: 908 518 0666
Fax: 908 518 1847
About the Author: Jerry Regan is manager, Technical Services, at Johnstown Wire Technologies, Inc., Johnstown, PA. Controls analysts Mike Cassidy, Ed Bauer, Wayne Kinnel and Dennis Frombach, from the JWT instrumentation and controls group, assisted in preparation of this article. Cassidy is the controls analyst with responsibility for the mill's environmental concerns.