From Reactive To Proactive
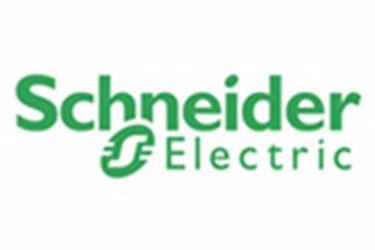
The Water Online editorial staff sat down for a brief chat with Lou Arone, Schneider Electric’s US Manager of the System & Architectures Team, Industrial Automation Business, as well as Vincent Puisor, Schneider’s Business Development Manager for Water & Wastewater in the Americas Region, to discuss water industry challenges and the solutions that Schneider has to offer. Below is our conversation, lightly edited for clarity and length.
Water Online: What's the biggest challenge that you see in the industry?
Vincent Puisor: We see aging infrastructure as one of the biggest pain points of our water and wastewater installations as they are reaching the end of their useful life.
Sustainability and resilience are aspects that we need to look into, especially with all the unprecedented weather conditions associated with climate change.
And, finally, aging workforce, as we will have a lot of people retiring in the next years and we need to make sure we transfer their knowledge to the new generation joining the field.
Water Online: What effect do you anticipate from federal infrastructure funding, and what should get highest priority?
Vincent Puisor: The funding that is being proposed is a great opportunity to upgrade our water and wastewater infrastructure. Highest priority should be focused on communities that are the most at risk and we should look into how we can accelerate water-reuse, water-loss, and energy-efficiency projects.
Another important aspect will be to build future-proof plants and networks and to take advantage of the digital transformation and the tools that exist today to make sure we build sustainable and resilient systems.
One of our challenges will be to make sure we take advantage of these new technologies and we do not build plants like we did 25 to 30 years ago. These systems need to be sustainable and smart.
Water Online: What role you do see technology and innovation playing in advancing the industry and solving current water challenges?
Vincent Puisor: It’s an exciting time to be in the water & wastewater industry, because now we have access to technology that we never had before and for a reasonable price because they are developed on the cloud. All the cloud-based predictive analytics are allowing us to move from reactive to proactive. These tools based on operational efficiency help us operate all these facilities more efficiently and to overcome challenges such as retention of the workforce.
Because these tools are in the cloud, cybersecurity becomes a critical aspect that needs to be addressed and managed.
The COVID situation has accelerated this digital transformation a lot, since everything is remote.
Water Online: Tell us about yourself and your company.
Vincent Puisor: At Schneider Electric we are very proud to be ranked as the most sustainable company in the world.
Through our strategic partnership with AVEVA, we create digital transformation solutions that combine energy management, automation systems, and services with industrial software.
I am responsible for business development in the Water Segment, with a focus on building solutions for customer needs.
Schneider has been present in the water industry for many years, and our solutions can be found in many utilities across the U.S. and around the world.
Water Online: Schneider Electric just released their “next generation” automation platform. How is this different from standard PLCs in the market today?
Lou Arone: EcoStruxure Automation Expert (EAE) is our “next generation” automation platform, which was released globally earlier this year. This represents a major change in controls on the factory floor. There has been a lot of talk around the Industrial 4th revolution, IIoT, and smart factory over the last few years. But when you look at the factory floor and PLC control, not much has changed. The time is right for a fundamental change to take place on the factory floor. So, ask yourself, what will the factory floor look like in 5 to 10 years when smart devices are ubiquitous? Smart connected devices could one day span from the push buttons to instrumentation to motor starters. Everything is connected. So, in a world where everything is connected, what does the PLC look like? Probably a lot like a switch — no real IO, just Ethernet connectivity.
Now follow this concept… If all the devices in the field are smart, and we need to control a tank level with a VFD-controlled motor, why do I need the PLC to poll the level sensor for information only for the PLC to send information to the motor? Why not have the level sensor talk directly to the VFD? This is the essence of EAE — pushing the control to the edge. This is smart devices talking to other smart devices. You program the system just like you do today but assign logic to run in devices at the edge. Today, this is not possible with the “one project” per PLC model. Today, our first release includes edge control devices that run in a medium-sized Modicon PLC (M251 dpac), Modicon high end PLC (M580 dpac), Altivar VFD (ATV dpac), and softPLC (soft dpac) The soft PLC can run on any PC; it can even run in a virtual machine on a blade server or raspberry pi device…very flexible). The software is built on the IEC61499 standard, which makes the promise of Universal Automation a possibility. EAE was built to take advantage of Universal Automation and create a giant step towards the “real” smart factory.
There is much more to talk about regarding EAE which our time today does not allow. The software has a built-in optional HMI and Historian, so the software begins to look and feel like a DCS system. But these are optional, and many customers will choose to stick with their existing SCADA systems. We communicate to all HMI and SCADA systems just like you do with your existing systems via OPC-UA. If this sounds interesting, or you’re interested in hearing more about EAE, feel free to contact me at Louis.Arone@SE.com.
Water Online: What is Universal Automation?
Lou Arone: If you were to ask a customer about their PLC or PAC control on their factory floor, many or most have standardized on a specific vendor platform. Over the years, they have done this because of the expertise the user may have with their existing staff and/or the cost to maintain spare software and support from multiple vendors. So, their solution is to standardize on one platform. The downside to this approach is that the customer is locked — locked to the technology and innovation that a single vendor can provide, locked into that vendor’s software, and locked into that vendor’s pricing. Can you imagine a world when an industry-wide factory floor standard exists that governs how all control software, hardware, and smart devices are programmed and communicate? A standard that allows the customer to plug and play with any vendor — this is the promise of Universal Automation. This puts the onus on the vendor to manufacture innovative best-in-class products and solutions for the marketplace. This is exactly what the IT world has accomplished many years ago. Now it is time for the factory floor. To know more about the Universal Automation movement go to www.UniversalAutomation.org.
Water Online: How much of a challenge is ‘vendor lock-in’?
Lou Arone: We have been so used to the very proprietary world of factory automation that many don’t see it as an issue. But when you think of your private lives, half of us live in an Apple universe and the other half Android. Home automation adds a third player, Amazon (Alexa). Some of these devices do not play well together, so you tend to stick with one sphere. The same is true for the factory floor. Customers tend to choose one PLC vendor…and now they are stuck with that vendor. Your locked in. This stifles innovation and limits the customer to only that vendors options. Today your PLC is configured using a software from the manufacture of the PLC you are going to use. You as the consumer have no choice; you must use their software and their hardware. The hardware and software are tightly coupled together. The promise of universal automation separates the hardware from the software. The promise is that all vendors will create smart products (hardware and software) that adhere to the IEC61499 and Universal Automation standard. This will create an environment where the customer can choose best-in-class products from any manufacture.
Water Online: How will EcoStruxure Automation Expert benefit those in the WWW industry?
Lou Arone: EAE will benefit everyone — the end user, the OEM, and the integrator. From the end user perspective, EAE drives towards future-proofing the systems by decoupling the software from the hardware. Once this is achieved, the end user is free to add and replace any device that is Universal Automation compatible. This allows you to choose best-in-class devices that have the features that you want. Let’s take the example of an oil refinery. I realize that this is an extreme, but it gets the point across. If an oil refinery has 40 plants around the globe, and they need to upgrade their automation systems every 20 years (on average), that means they are doing a major modernization project every six months. The downtime required to replace both the hardware and the software is huge. Lost revenue, increased risk, AND at a huge cost. They need to replace both hardware and software. Yet once complete, they are manufacturing the same products in the same way that they did before the modernization. They already owned and paid for the intellectual property, yet they need to pay someone to reprogram the new hardware. If the system were a Universal Automation system, that customer could keep his intellectual property (PLC application) and replace the individual automation hardware components one at time as necessary. The same logic gets downloaded into the new smart device. No need to rewrite or reengineer.
From the OEM machine builder perspective, the OEM’s main job is to produce a machine. Unfortunately, today they are being asked to supply that same machine in multiple versions — one with Automation PLC Vendor A, PLC Vendor B, and PLC Vendor C. Now they need to have expensive expertise on staff to know the solutions for Vendor A, Vendor B, and Vendor C — all of which are different, unique, and program in their own proprietary software. This is a very costly expertise that the OEM does not really care about; they just care about making their machine do what they said it would do. In the world of Universal Automation, the OEM only needs to write one program. The code will execute on any Universal Automation device. When the machine is delivered to the customer, he just hands him the application. The customer can then run the code in any Universal Automation hardware, including any smart device that may be supplied by the OEM. The interaction (OEM to end user) is greatly simplified, and the OEM can focus their money and resources towards innovation of new products and solutions, not on having multiple versions of the same machine.
Water Online: What are the industry challenges that your company and its solutions designed to address?
Vincent Puisor: The water industry is facing a number of significant challenges like aging infrastructure, while at the same time facing unprecedented weather conditions associated with climate change, and these challenges are creating an environment where the resilience of our water and wastewater facilities becomes critical. Our solution helps build resilient systems, and digital transformation allows us to go from reactive to proactive.
Aging workforce is something we continue to address with digital transformation. This will allow us to transfer information from the retiring workforce, who have all the knowledge, to the new people joining the industry.
With all the tools that we have from connected products to apps and analytics, we can help the industry with the complete water cycle.
Click here for more WEFTEC interviews and content.