Expanding Industrial Applications For Automation In Pumping
By Sally Cogan and Bella Works
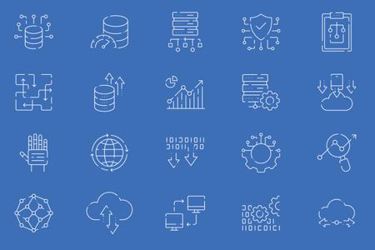
The Internet of Things (IoT), Industry 4.0, and connectivity in drives is the future, and many market segments must modernize to compete. The world is more connected than ever with new technological advances that produce higher process efficiency and time savings. To stay competitive in this environment, companies must include automated solutions such as remote management, monitoring, and control.
Real-time data insights are allowing users to have accurate data analytics to make informed, critical decisions. This same expectation is making its way into the pumping industry such as agriculture, oil and gas, and wastewater. One solution is remote management of drives. Drive connectivity allows users to access data from a variable frequency drive (VFD) to monitor equipment, track trends, and store their data in a wireless cloud. Users can access real-time data from their VFD from anywhere at any time. They can also make informed decisions and change run patterns remotely based on data collected. Using remote management of equipment in pumping applications can help organizations modernize with the technological advances and remain a competitive option in the marketplace.
The benefits of remote management for drives are vast and applicable to different pumping industries. First, automating processes can help reduce manual errors that occur from human error. Automation also reduces the likelihood of injury on the jobsite by adjusting remotely. Labor savings and increased productivity are paramount for industries with small operating profits. Remote management of drives saves time by allowing users to view production and change settings remotely. Employees can spend less time on maintenance checks and travel and more time where it matters most.
Higher productivity can save countless hours spent manually checking equipment that is operating properly. Another benefit of remote management is reducing downtime and improving the efficiency of uptime. When errors are detected, alerts (push notifications and emails) are sent directly to the technician in real time and service support is available through application platforms, email, or by phone. Finally, remote management gathers data and uses historical information to provide insights on VFD run history. Applications such as Eaton’s Control Xpert interpret data that is stored in the cloud to provide reports to better inform users of how their system is running. Making data-driven decisions will improve efficiency and build continuous process improvements. While there are potential drawbacks to increased automated connectivity in pumping, the benefits far outweigh them.
Automation in Agriculture
For example, agricultural users can utilize remote monitoring and control in a variety of different ways to help improve process efficiency to produce a successful and profitable harvest. Through remote monitoring of pumps and irrigation systems, agricultural users can remotely view the status of their equipment. They can also see in real time if their pumps are running properly and can monitor their equipment from anywhere via cellular connectivity (cellular gateway).
Additionally, they can control their pumping equipment remotely; users can start, stop, and change the speed of their VFDs from anywhere on their mobile device. Another advantage to using remote control of pumping equipment is that users can schedule in advance when to start and stop their pumps. Further, with changing regulations, remote management can be a best practice for water-usage mandates in times of drought or to meet state and local regulations.
Automation in Oil and Gas
Users in the oil and gas market can also benefit from adopting IoT technologies in tandem with their VFDs. For instance, field operators in the oil and gas market can enable remote site management of their facility to improve process efficiency and generate real-time data insights in the form of reports to help optimize processes, including well flow. Within the oil and gas market, remote management of pumps can be used for a variety of different applications, such as upstream pumping, gathering sites, and at midstream stations.
Remote management in the oil and gas segment can include remote control of multiple devices/pumps, creating pump schedules to go on and off at certain times on designated days, and generating data reports to monitor outputs and always be notified on the status of pumps via push notifications and emails. One example of monitoring in upstream oil and gas that could benefit from mobile remote management is monitoring and controlling pumpjack motors. These are often located in remote areas, far from each other. Remote monitoring can save transportation time and increase the opportunity cost associated with labor savings. Finally, technological advances as well as analytical data insights can improve operational efficiency by recording information regarding the power quality of upstream pumping and alerting users of outages.
Users are demanding automated, data-driven, remote solutions, including in the pumping industry. And organizations need to push for digital solutions paired with VFD connectivity to meet this demand, whether it’s for general pumping applications, agriculture, or oil and gas. The technological advances of IoT can help improve operational efficiencies and reduce operating costs while remaining a strong competitor in the digital landscape.
Sally Cogan is Product Manager, Enclosed Drives for Eaton.
Bella Works is Associate Product Manager at Eaton.