European Vinyls Corporation: Case Study
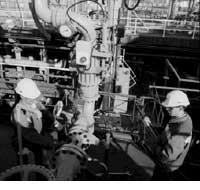
VOCs: the emissions challenge
New laws and new attitudes to environmental protection are driving down emissions of volatile organic compounds (VOCs). In 1997, the United Nations Economic Council for the Environment agreed to cut global VOC emissions by 30% by 2002.
The aim is to reduce the damage that VOCs cause to human health and the environment. Many of these substances are carcinogenic and a key cause of photochemical smog.
Individual countries are now following the UN lead. Germany's latest TA Luft regulations and the UK's Environmental Protection Act, for instance, set stringent discharge limits for VOCs such as monomers and organic solvents. Allowable emissions vary according to the source and nature of each VOC, but a typical value for Trichloroethylene, a common solvent, is 20 mg/m3.
Manufacturers handling VOCs have had to think seriously about how to meet these new limits. Some have been able to substitute water-based alternatives or non-volatile organic solvents, but often this is not possible. Traditional technologies for controlling emissions include adsorption on activated carbon and various methods of incineration.
However, the neatest and cleanest way to remove VOCs from exhaust gas streams is by condensation with liquid nitrogen. Using proprietary technology, Air Products' Cryo-Condap™ process removes VOCs to meet emission evels of 20 mg/m3, as well as overcoming many of the limitations of traditional emission-control methods. Cryo-Condap™ can be fully customised to remove most VOCs and to suit most process types.
Meeting the challenges of environmental legislation
European Vinyls Corporation (EVC) is a world leader in the manufacture of polyvinyl chloride (PVC), a commodity polymer used in almost every aspect of modern life. EVC employs more than 4000 people across Europe and India. EVC works closely with industry associations such as the European Council of Vinyl Manufacturers (EVCM), of which it is a founder member. EVC has signed the EVCM Industry Charters which set demanding environmental targets for the production of vinyl chloride monomer (VCM) and PVC.
Keeping VCM under control
Vinyl Chloride Monomer (VCM) manufactured at the Runcorn site is exported by ship to other EVC plants in Europe for conversion to PVC. Occasionally VCM can also be imported by ship to cover a prolonged shutdown of the Runcorn PVC plant. The shipping terminal is located at the Runcorn layby of the Manchester Ship Canal and is linked by pipeline to the production plants. To comply with Environment Agency regulations, it is necessary to limit the release of VCM to atmosphere to a total emission of 0.1 kg during the removal of VCM liquid and vapour from the marine loading arm, following the filling or emptying of a ship. By using the Cryo-Condap™ cryogenic VOC recovery system, EVC is able to achieve results significantly lower than this value.
VCM is pumped into the ship's cargo tanks through an articulated loading arm. Once loading is complete,the VCM vapour remaining in the loading arm and its associated pipework must be removed, both to protect dock workers and to meet UK emission regulations. The challenge was to find the quickest and most effective way to achieve this within the 1 hour time slot. The actual time achieved, including disconnection of the loading arm is 45 minutes. EVC Senior Process Engineer Mike Newman comments: "With the terminal 3km from the main plant, we wanted a recovery system which would meet all our recovery requirements whilst operating independently from the plant. We also needed a source of nitrogen for purging the pipework."
Why cryogenic condensation?
The Cryo-Condap™ cryogenic VOC recovery system, designed and supplied by Air Products, combines the refrigeration power of liquid nitrogen with the inerting properties of nitrogen gas. The result is a skid-mounted VOC control system that is simple to install, economical to run and highly effective.
At temperatures down to -196oC, liquid nitrogen removes most VOCs almost completely. Solvent recovery performance is typically better than 99.9%, giving discharge concentrations sufficiently low to meet even the most stringent environmental standards. The graph below illustrates the reduction in concentration of vinyl chloride in nitrogen gas as the temperature of nitrogen decreases.
Compared to other abatement technologies, the capital cost of the equipment is low.
Recovered VOCs can often be re-used directly — something that is more difficult with adsorption systems and impossible with incinerators or catalytic oxidisers. Another factor that helps keep running costs to a minimum is the ability to re-use the nitrogen. Sites handling VOCs commonly use nitrogen to purge and blanket pipework and tanks; nitrogen gas recovered from the Cryo-Condap™ process is effectively free.
Air Products has over 50 years of cryogenic experience and has installed more than 50 Cryo-Condap™ systems worldwide.
Designing and installing
EVC provided Air Products with a performance specification for the VCM recovery process. After the ship has been docked,the loading arm, initially containing a VCM atmosphere, is purged using nitrogen gas.Purging must continue until the concentration of VCM in the loading arm is sufficiently low to minimise risk to personnel when the arm is disengaged. Purging is calculated to require 100 volume changes before acceptable concentrations can be achieved prior to disconnection. This was calculated for EVC by Air Products. The purge gas is treated in the Cryo-Condap™ system, VCM condenses and is recovered. The cleaned purge gas, which now meets environmental legislation, is vented to atmosphere. The gas, evolved from the liquid nitrogen used as the refrigerant in the Cryo-Condap™ system, also provides a cost effective source of clean gas for purging. Air Products [senior engineer] Nanna Heiberg says: "In theory the solution was simple enough: a Cryo-Condap™ system to condense the VCM requires only a carefully-designed heat exchanger. However, the installation and control package surrounding the heat exchanger is key to providing a system which is operator-friendly and integrates with the total site."
Air Products used its own in-house modelling software to design a system to meet EVC's current and future needs. The heat exchanger and gas handling systems are custom designed and all fit on a single compact skid.
Detailed site engineering and equipment procurement was done by Simon Carves, a company that for over 100 years has provided engineering and project management services to the process industries. For this project Simon Carves worked as a sub-contractor for EVC.
"Ideal for our requirements"
Once the new system was commissioned, EVC was able to use it to remove VCM vapour far more easily than would have been possible using remote incineration. The cryogenic installation has the benefit of recovering VCM efficiently, enabling a complete purge of the loading arm within two hours, thus minimising the turnaround time of the ship.
Mike Newman is pleased with the results."This system is ideal for our requirements, especially for a remote operation such as at the Runcorn terminal where the full range of services and a permanent operator presence are not available," he says."Since our needs are intermittent, it is essential that we are able to turn the system on and off as required and have rapid recovery to suit the requirements of the docked ship. Any delay in the system working would lead to a delay in loading - which in turn could mean the ship being docked unnecessarily for over 24 hours."
"We are very happy with the system at Runcorn and it has met all our requirements. As for future installations, we would certainly install the Cryo-Condap™ system where flexible VOC recovery is required. It is an ideal solution for bulk carriers that have to load at a location remote from the manufacturing plant."
Air Products and Chemicals, Inc., 7201 Hamilton Boulevard, Allentown, PA 18195-1501. Tel: 610-481-4911; Fax: 800-880-5204.