Environmentally-Sustainable Induced Air Flotation From CST Wastewater Solutions Opens New Markets For High-Temperature Fats And Solids Recovery
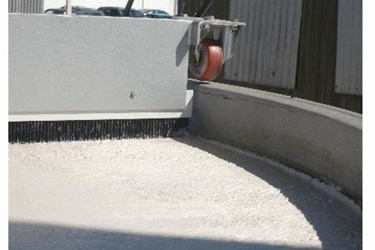
A highly effective flotation cell that allows fats and solids recovery in high-temperature applications has been developed by Australasian and Asia-Pacific wastewater treatment specialist CST Wastewater Solutions Pty Ltd.
The company’s new Induced Air Flotation (IAF) technology is a major advance on one of the world’s most preferred and simplest flotation technologies for industrial applications, Dissolved Air Flotation (DAF).
DAF is a tried and trusted treatment of industrial wastewater effluents produced by food, beverage and primary processing plants, but it has shortcomings when applied to demanding high-temperature applications for which IAF is purpose-designed, including:
- Treatment of high-temperature rendering waste in meat works.
- Clean in Place (CIP) wastewater in food factories.
- Quenching liquors in coke ovens applications.
- Oil and grease removal from hot solutions, such as rolling mills.
“Applications for which DAF is suitable are integral to the economies of many countries in Australasia, Asia, Africa, America and Europe, says CST Wastewater Solutions Managing Director, Mr. Michael Bambridge. However, in high-temperature applications (ie wastewater above 80oC), DAF has a number of limitations, including:
- The solubility of air is very low, so very high recycle ratios are required.
- Cavitation is a problem in recycle pumps.
- Higher saturator pressure is required.
- Large cells are needed to accommodate increased recycle flow.
CST Wastewater Solutions overcomes these problems by introducing an energy- efficient IAF High Temperature Cell to provide a different method of introducing pressurized air into the flotation process.
The high-temperature IAF cell uses a spinning disk to provide pressurized air for vortex bubble formation in the volumes required in high-temperature applications.
The flotation cell is based on a multistage separation process, graphically depicted below, with an innovative internal launder to ensure the float product produced from the cell remains at the same temperature as the liquid, so as to facilitate sludge transfer.
This is essential to the efficiency of the system in overcoming previous barriers to high-temperature flotation,” says Mr. Bambridge, whose company is widely experienced with DAF systems over more than 25 years. His company produces DAF and, where required, complementary environmentally efficient anaerobic digestion systems for cleaner wastewater and local electricity production for major meat, food and beverage operations.
To ensure the practicality of the process for particular applications, CST uses a pilot IAF cell to assess the technology’s efficiency, scalability and design data, says Mr. Bambridge.
“DAF’s great strengths as a primary treatment include relative simplicity in installation and proven cost-efficiency in separating oil and suspended solids from wastewater in applications as diverse as dairy, beef, pork poultry, grains, cereals and crops such as beets, cassava, potatoes, soy, wheat, corn and sugar cane. Compact and robust DAF systems achieve environmental sustainability by reducing Chemical Oxygen Demand (COD) loading by the removal of high COD contaminants including fats, oils and greases, color, organic matter and colloidal material.
“The new IAF technology extends the efficiency and environmental sustainability benefits into new markets, by extending the capacity of flotation systems to generate bubbles at temperatures above 80oC, the usual limit for DAF systems. This opens up the potential for new levels of efficiency in high-temperature applications, which also benefit from reduced energy consumption.
“By eliminating bubble solubility issues at higher temperatures – including removing the need for higher pressures and larger cells – the new design is energy-efficient and sustainable over the longer term, as well as highly effective immediately upon installation in oil-water separation at elevated temperatures.”
For more information, visit www.cstwastewater.com.
Source: CST Wastewater Solutions Pty Ltd.