Energy-Saving In Water Systems: The Key To Cutting Costs And Achieving Net Zero
By Surendra Muppana
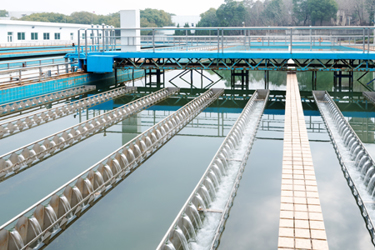
When seeking energy reduction and efficiency, start with your power-hungry pumps and the motors that drive them.
Many of us are lucky enough to be able to turn on a tap and have clean water start flowing. Behind this, and all sorts of other domestic, business, and industrial applications that enable our modern world, utilities must move and process incredible volumes of water. Moving this much water is extremely energy-intensive. Experts estimate that around 4% of total global energy production goes toward water and wastewater processing. That’s approximately equivalent to the total energy use of Australia.1
As the global population grows and the trend toward urbanization continues, demands on water and wastewater systems will also grow. This includes subsegments, such as water and wastewater treatment, desalination, and irrigation, all of which require significant amounts of energy.
Fortunately, even seemingly small-percentage efficiency improvements in these vital industries can add up to huge energy savings on a global scale.
Why Are Utilities Seeking Greater Efficiency?
The current approach is not scalable or sustainable in the long term. Meeting demand relies on making water and wastewater infrastructure more energy-efficient. This is in line with the society-wide push for sustainability. Legislation such as the EU’s Green Deal, for example, sets minimum efficiency standards for multiple industries, including the water industry. Achieving net zero will require a combined effort from all industries, and efforts to increase efficiency are a valuable contribution.
Industrywide adoption of modern, high-efficiency technologies will enable the industry to meet its sustainability commitments and equip it to serve a growing population. Energy accounts for an average of 45% of the total cost of providing water, so utilities that adopt more efficient technologies will be able to maintain profitability.2
Here are some actionable steps that utilities can take to make operations more efficient.
Switch To High-Efficiency Motors
Centrifugal pumps, the heart of most operations in the water segment, are driven by electric motors. These motors are responsible for over 90% of electricity use in water facilities.
Often, utilities run motors to the end of their working life. This means that older, less efficient units, such as IE1 and IE2 efficiency class motors, can be kept in place for decades.3 In the time since they were installed, technology has advanced and motors have become more efficient. Each new IE class motor reduces losses significantly over its predecessor — an IE4 motor, for example, has 20% lower losses than an IE3 motor.
Many utilities are already using ultra-premium IE5 synchronous reluctance motors (SynRMs), wherever feasible, in order to enhance their operations efficiency. Further, the return on investment on such advanced solutions is typically achieved within two years.
Adopt Variable Speed Drives
In many cases, the motors that drive centrifugal pumps and other key equipment do not need to run continually at maximum speed as the demand for water varies during a 24-hour period. Peak use occurs during daytime hours, while demand is lower at night.
To reduce the flow of water, mechanical methods such as valves and throttles are often used. This is similar to a driver applying the brakes in a vehicle to regulate speed while keeping the other foot on the accelerator.
An efficient and well-proven alternative is to use a variable speed drive (VSD) that regulates the speed and torque of the motor — and thus, the pump output — that equals the flow of water. This flow control with VSDs would reduce considerable energy consumption, as the power consumed by the centrifugal pumps is proportional to the cube of its speed. Moreover, improved flow control with VSDs would ensure the pump operates at its best efficiency point (BEP).
Modern VSDs also include flow-measurement and energy-monitoring functions, enabling facilities to develop a clearer understanding of energy use. Reduced energy use can be calculated in terms of kilowatt-hours, as well as in CO2 emissions eliminated and money saved.
These energy savings are so substantial that the return on investment on VSDs is typically paid off within one to two years. In addition, by ensuring the soft starting and stopping of the system, VSDs help minimize mechanical and electrical stresses and, in turn, extend the life of motors and pumps and improve the plant’s overall productivity.
Water pumps at the Saneago site.
Increasing Efficiency The World Over
These energy-efficiency benefits have been demonstrated worldwide. In the Brazilian state of Goiás, the utility Saneago provides drinking water to over 5.7 million people. The company hired a consultant and identified that electricity was consistently one of the company’s top expenditures, and that most of it was going toward powering pumps. To save costs, Saneago set out to replace these motors.
Saneago worked with ABB to install high-efficiency motors and drives throughout its facilities. The changes reduced the utility’s electricity consumption by 25%.
The new water and wastewater drives have intelligent multipump functionality. This means that they can control multiple pumps simultaneously to meet flow and pressure requirements based on real-time data from sensors. They also installed remote condition monitoring tools at four inlet water pumping stations.
Osmar Qualhato Júnior, Saneago’s energy management supervisor, said that by “being a pioneer in utilizing this type of technology in Latin America, we have moved Saneago into the era of digitalization … this has saved us much time, money, and trouble.”
Across the Atlantic in North Rhine-Westphalia, Germany, the Bocholt sewage treatment plant was also looking to cut energy use. It used six pumps at a pumping station, but analysis determined that they could be made more efficient.
The wastewater facility made significant changes to the impeller geometry, which improved both the electrical and mechanical efficiency. As a result, the demand could be met with just four out of six pumps. In addition to reducing the number of motors, the Bocholt facility decided to use high-efficiency SynRMs, which must be paired with VSDs, to further reduce energy usage.
The system can now automatically adjust return sludge flow based on hydraulic load. Any time that the pumps are not operating at full capacity, the facility is using less electricity and saving money. Thanks to this modernization, the Bocholt sewage treatment plant has cut energy consumption by 40%.
Efficiency Makes Business And Environmental Sense
Energy-intensive processes are required throughout water and wastewater facilities. Optimizing these systems for improved energy efficiency saves money and reduces emissions.
An impactful change that facilities can make is adopting modern high-efficiency motors with VSDs. This alone cuts energy use up to 25% or more, taking a major chunk out of a facility’s operating expenditures. The resulting energy savings quickly exceed the cost of the improvements, leaving the facility with lower energy costs and bringing the industry closer to net zero.
References:
- IEA World Energy Outlook 2018, Page 122, https://iea.blob.core.windows.net/assets/77ecf96c-5f4b-4d0d-9d93-d81b938217cb/World_Energy_Outlook_2018.pdf
- Water-Energy Nexus, World Energy Outlook Special Report, 2016, page 30, https://iea.blob.core.windows.net/assets/e4a7e1a5-b6ed-4f36-911fb0111e49aab9/WorldEnergyOutlook2016ExcerptWaterEnergyNexus.pdf
- In Europe, China, and several other countries, motor efficiency is measured by European IE (International Efficiency) class. A higher IE rating means that a motor is more efficient, and each increase in number (such as from IE3 to IE4) represents a 20% decrease in losses.
About the Author
Surendra Muppana is the global water segment manager for ABB Motion. To learn more, visit https://new.abb.com/water.