Efficiently Treating Wastewater And Increasing Opportunities For Your Systems
By Rhonda Landis
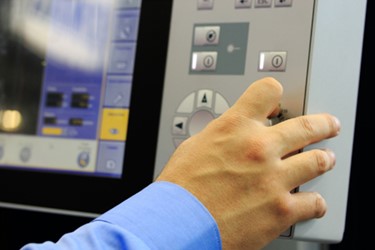
Analytics and automation offer a pathway to time, labor, and energy savings while improving regulatory compliance, resiliency, and emergency response.
The largest issues today in the wastewater industry are visibility into data and processes, the availability of knowledgeable staff with the expertise to understand how to identify and resolve issues, and rising energy consumption and costs. These issues alone necessitate the use of automation tools. However, today’s additional considerations for safety and environmental factors and footprints compound the concerns and require an easy way to monitor, understand, and identify solutions to these real-world everyday problems.
What Are My Options?
Continuous monitoring and intelligent alerting solutions provide 24/7 remote and real-time visibility into all your data, with notifications sent appropriately when corrective actions are required. By collecting and normalizing data from multiple sources — vendor-agnostic sensors, SCADA systems, and historians — operators can now monitor data trends and avoid issues proactively, before they turn into big problems.
Gone are the days when operators had to sit in a control room in front of a terminal, make unnecessary emergency drives to the plant, enter non-instrumented data on clipboards, or log in through a slow, remote-access VPN. Continuous water monitoring now enables all users to participate and ensure water quality by instantly knowing the chemical and solid levels from any internet browser, tablet, or smartphone — virtually anytime and anywhere.
Monitoring of surface water for pH, conductivity, turbidity, and other necessary data, against the minimum and maximum thresholds, can now begin to detect abnormal trends in the data, long before an issue comes to occurrence.
Operational Efficiency Is Attainable
To achieve increased operational efficiency in your systems, you can start by eliminating unnecessary manual effort. Any data that should be monitored, but is not currently instrumented, has historically been entered on paper and later fed to a SCADA system. If the manually entered critical data exceeds the threshold limits and requires action, this information is not known for hours or even a day later. This can result in environmental and safety issues as well as regulatory non-compliance.
Manual data entry (MDE) allows immediate access to the non-instrumented data for immediate analysis and immediate notification of critical issues. This remotely entered data can be entered and saved without access to cellular data or Wi-Fi and, once synced, can be used immediately in your continuous monitoring trending and analytics for further analysis. Coupled with fault detection and diagnostics, you will now gain operational efficiency while saving energy through smart analytics. Further, you can identify issues and notify your operators when actions should be taken, and provide the best solution to remedy the issue.
No more wasted trips or effort spent tracking down a false emergency. Water and wastewater operators can gain additional efficiency with a continuous monitoring package that includes detections of bad quality data, including sensor issues and flat-lined data. Having accurate and detailed information always available allows operators to quickly identify any data-quality issue with the sensors and act appropriately.
More Than An Alert Off A Threshold
Communication is vital between field technicians and local plant operators, and features like
Go-To-Action Chat allow instant contact with live messages tied to the faulty equipment, station, or plant. Integration with work order systems, predictive maintenance activities, and other sequence-of-operations functionality creates focus and prioritization on what is important and ensures that the appropriate actions are disseminated quickly, tracked, and resolved consistently, in the shortest timeframe possible.
Some of these fault detection systems can act as a “mini” work order system to prioritize and assign the work to be accomplished, or they can easily integrate with your own work order software to feed the corrective actions for scheduling. This allows users of these systems to move toward automation at a rate they feel comfortable with, gaining all the benefits of the new technologies while still allowing some manual control over the results as operators gain a level of comfort and trust with the system.
Stay Clean And Compliant
Regulatory agencies and utilities require access to specific data and/or anomalies in the data. Time and effort can be cut by providing private dashboards for those agencies to review the necessary data from their various customers, with all the anomaly detection preconfigured. These agencies can now access the necessary data, with the ability to export the data in .csv or .pdf format for their needs, without any customer operator intervention.
After achieving savings with manpower efficiency, the next-highest operating cost is the amount of energy used, and unfortunately the cost isn’t going down anytime soon. New regulations to tighten energy use are being implemented to combat climate change, which will only add to the existing cost structure. Ensuring that the plant is as energy-efficient as possible is the only way to offset these increasing costs. How do you gain energy savings while still achieving the necessary output? You must understand where you have excessive or unnecessary energy use.
Virtual metering, in the absence of meters, allows you to track large equipment energy consumption with options for reducing energy during peak demand periods. Continuous monitoring with fault detection analytics can leverage these virtual meters, along with your real-time meters, SCADA, historian, and MDE data, and provide recommendations for the optimal use of pumps, wells, and tanks, while achieving the necessary flow to provide the right output at the lowest-possible energy cost.
Looking Ahead To The Future
It's important to understand how water efficiency can help control the bottom line, and how new codes, standards, and regulations will change the way you are doing business. Continuous commissioning and fault detection software is the “next big thing” in the water and wastewater industry to increase efficiency up to 20 percent and save 3 to 5 percent on energy use, all while making your process — and your people — more efficient and effective.
As VP of Operations, Rhonda Landis is responsible for all operations and customer success at FacilityConneX (www.facilityconnex.com). Previously she led AutomaTech's Services Organization and held several senior engineering roles at GE Intelligent Platforms (formerly GE Fanuc).