Double Duty Flow Measurement: How To Conquer Changing Flow Conditions And Tight Footprints
By Matt Holmes, P.E., Director, Research & Development and Mike Dyer, Applications Engineer, McCrometer, Inc.
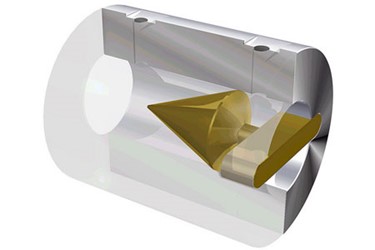
While accurate flow measurement is critical for most industries, flow conditions that change over time can make it difficult to properly size a flow meter. Replacing a meter as the flow changes is impractical and expensive. In addition, flow disturbers can greatly impact meter accuracy, so addressing that issue is important as well. A uniquely designed flow meter may be the solution to both problems.
Flow Velocity Profile Problems
Piping configurations, like elbows, tees, or reducers, create flow disturbances, as do valves and nearby pumps. Disturbed flow profiles can create large errors in the accuracy of some flow meters.
Flow meter manufacturers specify the amount of upstream and downstream straight pipe required for installation. This may be 5 to 10 or even more pipe diameters of straight pipe before and after the meter. By following the recommended installation requirements, the flow is “conditioned” and accurate flow measurements are obtained.
However, it may not be possible to construct enough straight pipe run, especially during retrofit projects. In these cases, flow conditioners in the form of perforated plates or tube bundles can be installed.
V-Cone® meters offer another option. These are differential pressure meters with a cone mounted in the center of the tube. The pressure difference between the static line and the low pressure created downstream of the cone is measured with two pressure sensing taps. One tap is placed slightly upstream of the cone and the other is located downstream of the cone. The pressure difference indicates the fluid flow rate using Bernoulli’s equation.
The cone reshapes the velocity profile, conditioning the flow before measurement. Even with no straight pipe, V-Cone meters maintain 0.5 percent accuracy of reading.
Changing Flow Conditions
For some industries, flows may change dramatically over time. Flow meters are designed for accurate measurement over a specific flow range. Once beyond the specified limits, accuracy is greatly reduced. However, installing a new meter may be costly and difficult. If the flow conditions are expected to change intermittently, a better solution is necessary.
Solving Two Problems At Once
For smaller applications with line diameters from 1 to 6 inches, a Wafer-Cone® meter offers cost-effective flexibility. A Wafer-Cone uses the same measuring principle as a V-Cone meter and has similar flow conditioning aspects. It needs straight run of only 1 to 3 pipe diameters upstream and 0 to 1 downstream. This makes the Wafer-Cone excellent for retrofit projects or small footprints.
While V-Cone meters measure low pressure through the cone, Wafer-Cones measure low pressure through the pipe wall. This allows the Wafer-Cone to provide changeable cones to measure different flow levels. Cones are easily removed and replaced in less than 5 minutes.
For instance, a process could start with an average flow of 100 gallons per minute (gpm). If, over time, the flow drops to 20 gpm, simply remove the meter and replace the cone with a larger one. Recalibration is not necessary, and the flow readings will again be accurate to ±1 percent of actual flow.
The plug-and-play direct mount, flangeless design saves space and is easy to install. With no moving parts, maintenance is simplified as well.
Wafer-Cone Applications
While Wafer-Cone meters are frequently used in the oil and gas industry, they are suited for industrial and municipal applications as well. Any application that measures fluid or gas can benefit from the Wafer-Cones’ simplicity and flexibility. Made of a solid billet of stainless steel, these meters are extremely durable.
For industry, Wafer-Cone meters provide the ability to change out the meter quickly and provide high accuracy with minimal pipe straight run. Many companies use these meters to measure cooling water for compressors. They are also excellent for steam measurement, with a much better turn-down than vortex meters. They provide an economical way to measure challenging flows in many industries, including chemical, food & beverage, plastics, pharmaceuticals, district HVAC, and textiles.
For municipal applications, Wafer-Cone meters provide cost-saving, flexible, and accurate flow measurement. In very dirty water, these meters are easy to remove and clean. They are also very cost-effective for measuring digester gas and flows from air compressors for aeration tanks. Another advantage is their ability to measure flows with entrained air accurately.
Technical Expertise For Making The Right Flow Meter Choice
Making the right decision on flow metering technology can save time and money while ensuring accurate flow measurement. Manufacturers’ representatives have the expertise to help engineers and managers make the right choice for accurate flow measurement. Contact a knowledgeable source to explore the best options for your application.