Do I Really Need A New Flow Meter?

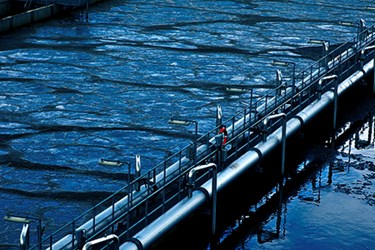
If you’re behind on flow meter technology, it’s understandable — wastewater monitoring and measurement devices have come a long way. Here’s your chance to catch up.
The measurement of flow in the wastewater industry is fundamental to the way the industry both operates and is regulated. We rely on it to understand stormwater volume and how much flow is passing through the treatment plant — and this, in turn, protects the environment and helps determine water quality standards.
Evolution Of Flow Measurement
The wastewater industry has been measuring flow for quite some time; the Lea Flow Recorder was introduced in the 1950s. It was a technology that had its day and was replaced by something newer, as happens with most technologies. At this point, some wastewater operators faced with the latest technology options may ask, “Do I really need a new flow meter?” After all, the wastewater doesn’t change much so why subscribe to a constant change in technology that costs a fortune to install and then has to be maintained?
But things do change, such as the nature of sewage treatment and the various technologies that wastewater facilities employ; thus, the techniques that we use to measure flow have changed as well. The industry innovates, and we measure flow more accurately. The need for this can be seen in the gigantic activated sludge plants that exist today where a 1 percent inaccuracy can result in hundreds, if not thousands, of dollars’ worth of cost (or earning) a day.
Since those days of the Lea Recorder, we have witnessed the development of ultrasonic technology. Most will remember the ultrasonic flow meters by Warren Jones, Milltronics, and other area-velocity-style units from companies such as Marsh-McBirney figure 1.
These technologies have developed over the years to be replaced by more modern and more accurate flow meters that are able not only to give flow measurement but also to provide a signal that will control various elements of the works.
Over the years, the needs of the industry have required flow meters to become more complicated and actually deliver more, making the flow meters that we have had redundant.
Flow Meters Today
Despite generations of technology design and evolution, there are just two types of flow meters that dominate the operational side of the water industry — ultrasonic flow meters and electromagnetic flow meters. Yes, there are also time-of-flight, area-velocity, and other flow meter types, but these two predominate, helped along by their own impressive development.
Take, for example, the case of the ultrasonic flow meter. The aforementioned Warren Jones flow meters (figure 2) were reliable and, in some cases, still work. These were replaced with technologies such as the Mobrey MSP90 (figure 3) and the Milltronics OCM III flow meter, which have been made redundant only in the past few years and have paved the way for the technologies by companies such as Pulsar Process Measurement (figure4) and Siemens.
Gradual changes in technology have allowed water companies to measure more accurately, do more with flow meters, and gain better control over operations. All this has been achieved with ultrasonic and electromagnetic flow meters alike, and the suppliers keep investing in R&D and pushing at the possibilities — to provide that much more to water utilities when they choose to buy the next generation of flow meters.
Innovation At Work
The application of flow meters has been addressed with a huge amount of R&D and innovation in the past 5 to 10 years.
The first area of innovation is flow measurement using area-velocity flow meters, both in-contact with the flow with Doppler and other methods and also in noncontact techniques. But what is the advantage? The main advantage is that a primary device such as a flume or a weir is not required; only a straight channel is required, instead, which means that construction costs can be reduced considerably. Although there are many contact area-velocity methods, the method that is probably in most use within the U.K. is the NIVUS wedge sensor for in-channel and in-pipe measurement. In the installation pictured (figure 5), the cost savings for the checking of an electromagnetic flow meter for verification purposes was in the region of £50,000 ($76,000), as opposed to digging a new chamber to use a time-of-flight flow meter.
The alternative in area-velocity measurement is noncontact measurement, currently growing in popularity in the U.K. due to its approval through the national verification scheme, MCERTS. The technique, based on the fundamentals of radar velocity measurement, was pioneered by Hach with the Flo-Dar flow meter and has been alternatively developed by ISCO with laser-based measurement of velocity and ultrasonic level measurement (figure 6). The advantages of the technique are threefold: There is no head loss in the channel (as there is no primary device); there is nothing in the channel to foul; and the installation can be performed in a few hours, with no disruption to the process.
This makes the technique suitable for open air chambers and also for applications like the sewer network — where it is not possible to use techniques that require a primary device (ultrasonic level) or a full-bore pipe (electromagnetics), both of which would be disruptive and costly to install. This is especially true on large-diameter pipes, where costs can be into hundreds of thousands of pounds/dollars, as opposed to a meter that is more expensive initially but perhaps cheaper in whole-life cost.
The second area of innovation is how you measure. Already mentioned are the different noncontact area-velocity techniques with radar technology versus laser technologies measuring flow velocity. Flow meter experts can argue the point as to which technique is better, and R&D scientists have worked hard developing and proving the techniques. As far as the purchaser is concerned, both techniques work. This development in technology is contested at the moment with a prime case of methodology measurement innovation — the tried-and-tested method of level-based flow measurement is being pitched against radar measurement.
A case study of the different techniques is pictured (figure 7), featuring radar level-based flow measurement (front in black) versus ultrasonic measurement (rear) versus a third, pressure-measurement technique (not pictured).
The ultrasonic, radar, and pressure meters were all set up by an independent flow measurement professional. The radar does not require solar shading and has the flow programming within the head of the device.
The trial among the three measurement techniques has been ongoing for eight months, and it shows that there is very little difference in readings among the three techniques (figure 8). Aside from standard operation (e.g., cleaning), there has been no intervention.
What did the test prove? Is radar better than ultrasonic? The answer is that both (or all three) of the technologies are accurate and can work. However, one technique may have an advantage over another in a particular application or operational setting.
So, “Do I Really Need A New Flow Meter?”
Yes! The more complicated part is figuring what to use and how to use it.
Throughout the years, different applications for flow measurement within wastewater have necessitated change; the need to automatically control with flow meters and/or measure more accurately brought about a refinement of measurement techniques that has provided greater efficiency. Different applications fostering different types of measurement will only continue as flow measurement moves out of its traditional area of the wastewater treatment plant and into the sewers — perhaps even into customers’ homes. The industry moves fast, but that’s no excuse to fall behind.
About The Author
Oliver Grievson is the wastewater flow & quality instrumentation specialist at the Foundation for Water Research, the director of the sensors for Water Interest Group, a member of the ICA Special Interest Group of the International Water Association, and founder of the LinkedIn Group “Water Industry Process Automation & Control” — all in addition to his duties as a flow compliance & regulatory efficiency manager. Working with other flow specialists, Grievson is preparing a wastewater flow manual for free release in late 2015, through the Foundation for Water Research.