Cost Management In Valve Selection: Balancing Price With Suitability
By Gilbert Welsford Jr.
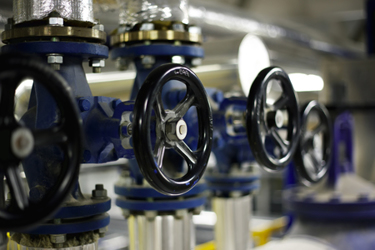
Because so many options exist, it’s possible to get safe and reliable performance from your valves without overspending. Matching valve specs to your application is the key.
Considering the multiplicity of valve types available on the market and the diversity of applications any one type can serve, proper valve selection can be a tricky proposition.
Even within a specific category of valve, differing styles, specific features, and manufacturers’ idiosyncrasies can all serve to complicate the matter.
Cost versus suitability represents an inarguably crucial factor that you can’t afford to overlook when choosing valves. After all, selecting a $1,000 ball valve for a certain application where a $500 alternative valve can perform equally well is hardly a prudent choice. Similarly, employing a cheaper valve with poor suitability for a high-risk application in the name of cost management proves equally unwise.
Additional caution is necessary while choosing valves for food processing units because some valves are manufactured with material that contains elements injurious to human health. There can be many direct and indirect consequences of poor valve selection, such as:
- Safety incidents
- Undue maintenance cost
- Capacity loss
- Energy loss
- Cost increment
- Product loss.
Valve Selection Basics
Process requirements
Specifying the correct valve type is a function of understanding your process requirements. Physical and chemical characteristics of the fluid being regulated play a key role in valve selection. The base material of the valve will depend on its compatibility with and suitability for the medium.
Carbon steel valves are often considered for most noncorrosive applications. Stainless steel valves are widely used in high-temperature and high-pressure corrosive applications. If you are choosing a valve for a corrosive application with a moderate temperature, plastic can be a great choice for you, as well.
Ball, plug, and globe-type valves are often considered when frequent adjustments in the process flow are required. On the other hand, gate-type valves are typically employed in binary on-off applications or for isolation purposes.
Operating conditions
Start with determining the temperature and pressure requirements. Find out about the pressure and temperature ranges where the valve will be deployed. Correct information about operating temperature, pressure, and other parameters will help you pick the right-sized valve. Installing an oversized or undersized valve can lead to operational troubles.
Valve manufacturers provide complete information about the maximum operating pressure and temperature of their products. Ensure that the valve you have chosen can withstand maximum operating conditions that may occur during process upsets and abnormalities. In the case of a check valve, it must be ensured that you have chosen a valve with a suitable cracking pressure rating.
Valve Materials — A Brief Summary
- Cast iron: Usually used for low-temperature and low-pressure applications.
- Ductile cast iron: Commonly used in oil, gas, steam, and water pipeline systems because of its broad range of operating pressures and temperatures.
- Stainless steel: Known for its remarkable durability and corrosion resistance, stainless steel is used in plenty of applications, ranging from general plant systems to the petrochemical industry.
- Bronze: Bronze is an alloy of zinc, tin, lead, and copper. Bronze offers great resistance against corrosion and wear. Its good machinability makes it a viable choice for complicated castings. Bronze valves are widely used in low- to medium-pressure services.
- Brass: Brass is an alloy of zinc and copper. It offers excellent machinability and forgeability and is cheaper than bronze.
- Cast Steel: Cast steel is commonly used in refineries, petrochemical, and oil fields because it tolerates a broad range of working pressures and temperatures.
Optimization Possibilities
Avoid expensive material when not required
You can secure tremendous savings by avoiding an expensive metal valve when it is not required for your process requirements and operating conditions. Plastic valves are often an ideal economical alternative, performing well in low-pressure and mildly corrosive applications. Valves made from stainless steel, brass, bronze, and other metals frequently cost more than plastic valves. However, they are not as durable and/or repairable as their metallic counterparts.
Coated vs. non-coated valves
A broad range of surface treatments and coatings is available for valves, and many vendors are offering valves with coated seats and other internal parts, such as polytetrafluorethylene (PTFE)-lined valves. However, lined and coated valves come at a higher cost, and these devices must only be chosen in cases where uncoated or unlined valves cannot withstand harsh process conditions.
Go with less expensive alternatives where possible
The availability of different valve types in different configurations and with different optional features has made it easy to cope with tight budgetary requirements in valve selection, while not compromising process safety. For example, consider non-rising stem gate valves, which come at a cheaper price than the rising ones. Both ball and butterfly type valves can be used in throttling applications, but the former one comes at a higher price. However, a ball valve is one of the most versatile types of valves, and researchers are continuously working on enhancing its optimization1 further.
Understand Valves As You Select
Valves are offered in a variety of types, and each type comes with a unique set of characteristics. Understanding different valve designs enables you to find the best type of valve for a process or project. The common types of valves include:
- Ball valve: These valves incorporate a ball to regulate flow. Ball valves come equipped with fast-acting quarter-turn handles and are known to be easier and faster to operate than gate valves.
- Butterfly valve: The wafer-type design and construction of the butterfly valve makes it an ultimate choice for tight spaces. You can find butterfly valve bodies in various configurations.
- Gate valve: In gate valves, linear motion is utilized to start or stop fluid flow. Generally speaking, these valves are not preferred for flow regulation and are used in fully closed or open positions.
- Globe valve: Globe valves are well-suited for applications where fluid modulation is required. T-body, angle body, and Y-pattern are the three available types of globe valves.
- Plug valve: Plug valves regulate flow through cylindrical or tapered plugs. These valves come with a 90-degree turn valve handle. Plug valves are good for high-temperature and high-pressure environments where tight shutoff is needed.
- Check valve: Check valves are self-activated valves used to prevent backflow in a line. Multiple types of check valves are available on the market, such as spring check valves, swing check valves, ball check valves, etc.
Function-based classification of valves
Valves can also be classified by function instead of design. The following are the most common functional designations used for valves:
- Isolation valves: Gate, pinch, butterfly, ball, plug, pinch, and piston valves
- Regulation valves: Globe, butterfly, ball, needle, plug, pinch, and diaphragm valves.
- Safety relief valves: Pressure safety (PSV), pressure relief (PRV), and pressure/vacuum relief (PVRV) valves
- Non-return valves: Lift and swing check valves.
Clarity on optional features
Commonly, many vendors offer “optional features” for which they charge separately. While buying budget valves, you must avoid wasting money on unnecessary optional features. As an example, consider “stainless steel handles,” which are often offered on an optional basis with ball valves. Yes, stainless steel handles are great, but any ordinary handle can do the job for you.
Valve repair vs. replacement
If you are seeking a replacement for a bad valve, you should explore valve repair opportunities around you first. Today, we have a very vibrant valve service industry available. There isn’t any generalized rule to determine whether a valve should be replaced with a newer one or be repaired. In some cases, you might be able to incur significant savings by getting a faulty valve refurbished by a reputable vendor.
Conclusion
The availability of valves in various materials and types allows us to make cost-effective choices. After choosing an appropriate type of valve (ball, butterfly, plug, etc.) according to the system’s requirement, you must establish which material will be the most suitable in cost and performance. Corrosiveness of atmosphere and process fluid must be kept in mind while choosing the material of construction, e.g., steel, cast iron, carbon steel, etc. Expensive “optional valve features” should be avoided when not required. Ensure that the products being considered are designed and manufactured in compliance with the relevant industrial standards, e.g., FM, UL, API, OSHA, etc.
Reference:
About The Author
Gilbert Welsford Jr. is the founder of ValveMan.com and a third-generation valve entrepreneur. He has learned valves since a young age and has brought his entrepreneurial ingenuity to the family business in 2011 by creating the online valve store — ValveMan. com. Gilbert’s focus is building on the legacy his grandfather started, his father grew, and he has amplified.