Computational Fluid Dynamics Hits Its Stride For Water, Wastewater, And Stormwater Treatment
By Srikanth Pathapati
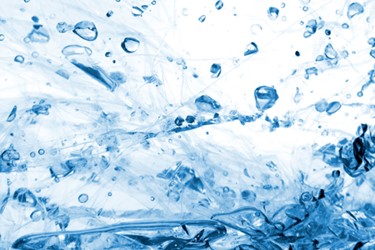
It took some time for computational fluid dynamics (CFD) to find its way to the water industry, but now that it has, a primer is warranted to understand its application.
For decades, computational fluid dynamics (CFD) has been the preeminent tool for design for astro/aero engineers at the Los Alamos National Laboratory, NASA, and Boeing, among many other giants. In the ‘90s, CFD was being strongly adopted by design engineers at the big car companies. Finally, CFD is coming home to the world of water, as civil and environmental engineers have slowly but steadily made steps in utilizing the powerful calculation and visualization tools available through multiphase CFD modeling.
The American Society of Civil Engineers (ASCE) has played a major role in encouraging the adoption of CFD in environmental and civil engineering applications. The society’s vision led it to develop protocols for applying CFD to the behavior of multiphase flows, as well as verification and validation of CFD models in those applications.
The goals of modeling for a civil and environmental engineer differ from, say, the needs of an automotive engineer, as do the scales of modeling. Civil and environmental engineers routinely have to design for large-scale structures and flows; multiphase flows including gas-liquid, solid-liquid, and liquid-liquid flows; and chemical and biological processes. For instance, while designing a contacting system for ozone disinfection, CFD at Mazzei Injector Company includes turbulence modeling, two-phase gas-liquid flow modeling, phase mass transfer modeling, and chemical species transport modeling — at actual scale. It is thus very important that there is a concerted effort to corral, test, validate, and organize modeling information pertinent to the field of water, wastewater, and stormwater treatment.
New Opportunities
In the last decade, technical papers using CFD started to appear in prominent journals including ASCE’s Journal of Environmental Engineering, Journal of Water Research, and Environmental Science and Technology, among many others. Some papers have even received prestigious awards from ASCE and the American Water Works Association (AWWA).
Computational fluid dynamics (CFD) modeling provides a highly detailed analysis of multiphase flows through this pipeline flash reactor (PFR). Improving CFD technology-enabled Mazzei to meet evolving customer requests with a new PFR+.
Other opportunities have also connected CFD with the world of water. A growing number of universities have started including mathematical modeling as part of the civil and environmental engineering curriculum. Commercial CFD packages previously tailored for mechanical and aerospace applications now include upgraded options for open-channel flows. Most recently, the first practically inclined textbook for CFD applications in civil and environmental engineering was published and released by the ASCE at the Environmental and Water Resources World Congress in Pittsburgh in 2019. A special issue of the Journal of Environmental Engineering focused on CFD is due in 2020 — this from a journal in which CFD articles barely appeared a decade ago!
I was fortunate to be involved with a group of seasoned engineering professionals and modelers in the writing of the ASCE primer, CFD Applications for Water, Wastewater and Stormwater, now available in the ASCE bookstore.1
Shining A Light
As far as tools for optimal design go, CFD is invaluable due to its all-important time and resource savings.
The Navier-Stokes (N-S) equations at the foundation of CFD modeling describe the motion of fluids. The N-S equations are also notoriously difficult to solve, being non-linear, partial differential equations. An entire field of numerical techniques to approximate a solution to the N-S equations has evolved in the last few decades: CFD.
To get a CFD model up and running, the engineer needs accurate drawings, solid models, operating parameters, material properties, robust software, and computing resources. This translates to working with designers, operators, consultants, academics, and salespeople. Outside of numerical accuracy, the engineer needs to incorporate verification and validation methodologies to ensure that the model is a flight of reasonable accuracy and not one of fancy.
The increasing body of work in CFD for water, wastewater, and stormwater is helping our industry validate models by providing more case studies in which we can compare CFD models with measurements of the finished, real-world projects that were designed according to the data. As I note in one of the chapters to which I contributed in Computational Fluid Dynamics: Applications in Water, Wastewater and Stormwater Treatment, models must be subject to verification (solving the equations right) and validation (solving the right equations).
Today’s powerful CFD tools allow engineers to model some of the biggest challenges limiting the efficacy of water treatment systems. For instance, we can model short-circuiting, which is a common issue for many contactors where the entire volume of the contactor is not utilized well, with flow taking a preferential path through the system. This can be a big issue for ozone contacting, where there is plenty of mass transfer but poor mixing.
Computational fluid dynamics (CFD) modeling reveals short-circuiting in this contactor, in which flows depicted in light blue and green hues take a preferential path through the vessel and fail to mix according to system requirements.
Increasingly powerful CFD capabilities have helped companies like Mazzei develop more effective mixing systems. For years, we used CFD modeling to determine the optimum size and positioning of mass transfer nozzles in our pipeline flash reactors (PFRs). PFRs are short lengths of pipeline with precisely placed nozzles to reintroduce and mix water from treated sidestreams back into the main flow. In response to customer demand for mixing systems that could replace static mixers without losing pressure while also adapting to high turndown rates, we developed our PFR+, an advanced pipeline flash reactor with vanes and a mixing grid that could combine gas and liquid phases as effectively as a static mixer with a fraction of the footprint and one-tenth the degree of pressure loss. The size, shape, and positioning of the vanes, as well as the design and orientation of the grid, were developed with the latest CFD modeling capabilities.
Avoiding Oversimplification
Today, a large number of water and wastewater treatment processes are designed using CFD. In fact, this is now often a requirement in many plant design specifications. The use of CFD can offer an excellent safeguard against oversimplification in the design of water, wastewater, and stormwater systems, which involve extremely complex realities of how water and gas flow and how gases react.
Simplification is often a practical requirement for macro-level problems. For instance, one does not need to worry about gradients localized to a cubic-inch volume when looking to understand the bulk flow of a river. On the other hand, typical simplifications — such as assuming ideal flow or plug flow behavior, using safety factors for dead zones and short-circuiting, ignoring the effects of a secondary phase such as gas on the primary flow, and assuming uniform water quality — are rapidly being challenged by increasingly challenging, complex applications and dwindling infrastructure and energy budgets.
The comfort of safety factors is often complicated by strained budgets and profits being cut due to overdesign. By allowing engineers to more accurately fine-tune their decisions, CFD can optimize design to protect margins and ensure performance.
The shift from back-of-the-envelope calculations to spreadsheets to sophisticated modeling is here. Why are we doing it now? Because the need is greater than ever. More realistically, because we can — we have the resources, the knowledge, and the market, as well as ecologically induced drive, at last.
Like any aspect of engineering, CFD continues to evolve. As we move into the future of engineering, a verification and validation procedure for CFD in environmental engineering needs to be codified, similar to how structural calculations are presently validated by a professional engineer. Fortunately, the future of CFD in the water industry is bright ... with vectors, contours, streamlines, and particle tracks.
Reference
1 https://ascelibrary.org/doi/book/10.1061/9780784415313
About The Author
Srikanth Pathapati is director of research and development for Mazzei Injector Company, LLC, a fluid design company that manufactures mixing and contacting systems. He holds a Ph.D. in environmental engineering from the University of Florida, a bachelor’s degree in electrical engineering from the University of Madras, and has over a decade of experience in physical testing, design optimization, and multiphase CFD modeling for unit operations and processes in water and wastewater treatment, oil and gas, and chemical process industries. He is active in the water/wastewater community and is a contributing author and panelist for the ASCE EWRI Primer for CFD in water and wastewater treatment. He can be contacted at spathapati@mazzei.net.