CMAR: A Project Delivery Method That Can Deliver For Water System Owners
By Sherri Leonard
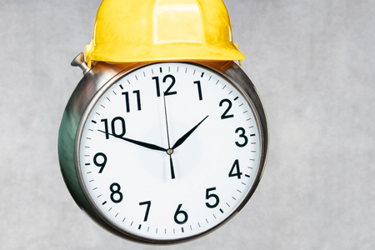
Learn the reasons why construction management at risk (CMAR) is gaining in popularity, and the specific benefits it offers.
Water system owners often have years to plan and build projects to replace aging equipment or deal with expected capacity changes. In such cases, they frequently use either the design-bid-build approach of project delivery, which entails contracting an architectural/ engineering firm to design the project and a construction firm to build it, or the design-build approach, which entails contracting one firm to both design and build it.
Occasionally, however, owners have to respond quickly to emergencies, such as damage to their physical plants or contamination of their water sources. In those instances, one possible solution is a project-delivery method called construction management at risk, which is commonly known as CMAR.
The city of Woodbury, Minnesota, turned to CMAR when it had to get a temporary water treatment plant up and running in six months after seven of its 19 wells were found to be contaminated with perfluoroalkyl and polyfluoroalkyl substances, or PFAS. My firm, Rice Lake Construction Group, was selected to be the CMAR on the project, which won an American Public Works Association 2021 Public Works Project of the Year award in the Disaster or Emergency Construction Repair category, $5 million to $25 million division.
CMAR’s Advantages
Like design-bid-build, CMAR involves contracting with both an architectural/engineering (A/E) firm and a construction firm. Instead of working sequentially, however, with the A/E firm producing a design that the construction firm then uses to build the project, the A/E firm, the construction firm, and the owner work together collaboratively, solving problems as they arise. Additionally, at some point, the owner negotiates a guaranteed maximum price, or GMP, with the construction firm. That feature is what gives CMAR its name because it puts the construction manager at risk for cost overruns.
In addition to cost, CMAR offers these other potential advantages over the design-bid-build and design-build approaches:
- Quicker delivery — CMAR can accomplish this because it enables the participants to work collaboratively rather than sequentially, which, among other things, allows them to order long lead-time equipment early in the process.
- Flexibility — CMAR makes it easier for participants to incorporate any design modifications required to complete the project as they work on it.
- Cost Transparency — CMAR requires the owner, A/E firm, and construction firm to work collaboratively through each step of a project from preconstruction to completion, which enables cost transparency by getting the owners involved in real-time decision-making.
Water System Owners, CMAR, And PFAS
How often water system owners use CMAR varies from region to region, but it is becoming more common due to the benefits it offers. Rice Lake Construction Group has completed over 75 projects using CMAR.
PFAS may force water system owners to consider using CMAR more frequently. Also known as “forever chemicals” because they don’t break down in either the environment or the human body, PFAS have been widely used in everything from firefighting foam to food wrappers and nonstick cookware, and, as a result, are popping up in water systems across the country. Additionally, according to draft toxicity analyses released by the U.S. EPA in late November 2021, there may be no safe exposure levels for at least two of them. That means that when water system operators discover PFAS in their water, they have to move fast to treat it, which can require them to get new water treatment plants built and online very quickly.
Woodbury’s PFAS Challenge
Woodbury found itself in that position in late 2019 as a result of a series of events that began two years earlier when it was notified by the Minnesota Department of Health that water from five of its 19 production wells exceeded a PFAS health-based guidance value and/or a health-risk index value, and that other wells were showing changes in detected PFAS concentration levels.
After the state of Minnesota received an $850 million settlement from a lawsuit it had filed against 3M Company for PFAS pollution, Woodbury secured a grant from the state to develop a mixing model of its distribution system so it could see how the impaired wells could affect its ability to provide clean drinking water to its residents. When it received the results of the model in late 2019, the city learned it was facing an impending crisis. The model showed it would have to use one or more of the impaired wells in order to meet the forecast water demand of its residents in the summer of 2020.
Fortunately, by then, the 3M settlement had enabled Woodbury to retain two companies, Advanced Engineering and Environmental Services (AE2S) and Jacobs Engineering, and begin working with them to plan how to deal with the PFAS contamination in its wells. In early January 2020, after learning what the model showed, Woodbury, AE2S, and Jacobs devised a plan that included designing, building, and operating a temporary water treatment plant (TWTP) that would serve the city for an estimated five to seven years, meet its near-term peak water demand, and provide it with time to develop a long-term water treatment solution.
The CMAR Solution
The plan called for having the TWTP operational by June 1, 2020, a little less than five months away. To meet that deadline, the city, AE2S, and Jacobs decided to use the CMAR project delivery method. The three stakeholders developed preliminary conceptual drawings and site plans of the TWTP, interviewed three potential CMARs, and selected Rice Lake Construction Group; and, on Feb. 7, 2020, they provided Rice Lake Construction Group with the first set of drawings and site plans, allowing us to establish a GMP for the project. Woodbury also used the first set of drawings and site plans to finalize its grant for the construction of the TWTP with the Minnesota Pollution Control Agency.
With that accomplished, the design team went to work on a final design for the TWTP. To expedite construction, it broke the design documents into three packages, the first of which covered the TWTP’s below-grade piping and foundation. On Feb. 20, 2020, that package was delivered to Rice Lake Construction Group and the Minnesota Department of Health, which had to make sure the designs met federal and state code. The documents enabled Woodbury to finalize its contract with Rice Lake Construction Group and issue its notice to proceed on Feb. 24, 2020. Rice Lake Construction Group began clearing the site that day.
The second design package to be finalized was the civil site package, which had to account for the TWTP’s proximity to a protected nature preserve. The package had to be done quickly to allow Woodbury’s engineering staff to review it, the local watershed district to obtain permits for the project, and Woodbury to solicit comments on the project. The Minnesota Department of Health approved a version of the second package with a 95 percent completion rating on March 6, 2020.
The final design package was the building package, which included all the architectural, structural, process, mechanical, and electrical construction details that normally would be included in a fully bid construction set. It was delivered March 9, 2020, and approved by the Minnesota Department of Health on March 17, 2020.
Additional Challenges
That left two and a half months to finish construction of the TWTP, which would have been challenging under any circumstances, but proved to be particularly so after the COVID- 19 pandemic erupted. Among other things, the project team had to be extra flexible to ensure the TWTP could be built on time and within budget using materials that weren’t affected by the supply chain disruptions brought on by the pandemic. The team also had to keep the number of people working on the project smaller than usual to enable social distancing and enforce other safety protocols to make sure no one working on the project caught COVID-19.
The team faced another challenge when water from another of Woodbury’s wells exceeded health index levels for PFAS, meaning a trunk line had to be built from that well to the TWTP. During the construction of the trunk line, an unmarked gas main was ruptured during directional drilling, forcing the team to spring into action in the middle of the night. The team worked with public safety officials and the local gas utility to make sure the main was repaired without incident by morning.
As if all that weren’t challenging enough, on May 25, George Floyd was killed, plunging the Twin Cities area, which Woodbury is part of, into civil unrest. That meant that security on the project had to be increased.
Success
Despite everything, the TWTP was completed by June 1, 2020, as planned, thanks in no small part to the collaboration enabled by CMAR.
“It can’t be emphasized enough how important collaboration and communication were to the success of this project,” said Jim Westerman, Woodbury’s assistant public works director.
About The Author
Sherri Leonard, director of collaborative delivery at Rice Lake Construction Group, is a 15-year veteran in construction specializing in large, complex, and collaborative projects in the water and wastewater industry. Sherri’s background is rooted in working with owners and engineers across the country on CMAR and design-build projects.