CCIT Solutions For The Pharmaceutical Industry
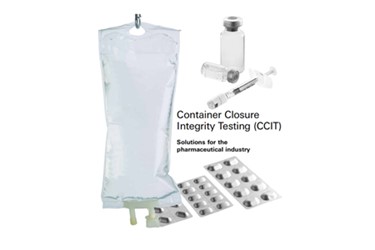
The quality, safety and effectiveness of drugs significantly depends on their proper packaging.
Container Closure Integrity Testing in the pharmaceutical industry – Challenges and Solutions
The quality, safety and effectiveness of drugs significantly depends on their proper packaging: Sterile products and moisture/oxygen sensitive drugs require excellent barrier during the shelf life of the product (up to a couple of years). The key risks for contamination are by humidity, oxygen or microbiological ingress, which can impact the drug stability throughout the product life cycle. To prevent the risks of stability failure integrity tests with a high sensitivity are required.
In a study that was published in 2000, the risk in regards to microbiological ingress related to different orifice sizes has been evaluated. As shown in figure 1 the critical leak size is at 0.2 µm, respectively 6·10-6 mbar l/s. This value is widely used as the so-called MALL (maximum allowable leak level).
This must be kept in mind when looking at other studies, which have proven that classical probabilistic test methods could miss leaks, resulting in an impairment of product sterility. Specific examples are Microbiological Ingress Testing as well as Blue Dye Test Methods. As shown in figure 2those methods only have an about 70% chance to detect a 10 µm leak. Any leaks below 5 µm are more or less non-detectable.
Click here to read report in PDF format
In 2008 the US FDA published a new guideline for the whole life science industry (pharmaceutical companies, veterinarian drugs and companies that manufacture sterile medical products) that obliges the sector to perform reliable physical measurement to ensure proper CCI. This guideline focuses on sterile and critical pharmaceutical products (e.g. vials and syringes) and is divided into 3 chapters:
- 1207.1: Package Integrity and Test Method Selection
- 1207.2: Package Integrity Leak Test Methods
- 1207.3: Package Seal Quality Test Methods
The USP thereby does not claim to describe all possible methods, but gives a good overview and general guideline for the evaluation of various popular potential methods.
The major reason for the large variety of different test methods is thereby that there is not the one test method that can cover all the needed quality checks that need to done during the development and production of a pharmaceutical packaging. In the early development stage of a packaging (“packaging design phase”), the packaging needs to be tested for defects at the MALL (maximum allowable leak limit), often in the range of 0.2 µm, respectively 6·10-6 mbar l/s. In comparison to that, a 100 % inspection of the production line that operates at speeds of 120 to 600 parts per minute, often runs tests with a much higher detection limit. The Limit of Detection (LOD) for production units is thereby defined on a risk-based decision between cost, technology and product. To compensate on this risk-based approach, additional off-line sample testing is performed to a tighter spec in the range of 1 to 10 µm. This also applies to stability testing which is performed in laboratory tests.
As an additional factor for the selection of the right test method, also the packaging and product type needs to be considered. Those are roughly divided into rigid and flexible packaging as well as liquid and solid drugs. Also characteristics such as transparency of the packaging and its electrical conductivity play an important part in regards to the selection of the right integrity test method.
Table 1 below gives an overview of available CCIT methods and also serves as a guideline for the selection by pointing out specific characteristics as well as limitations of the different test methods: