Can Electronic O&M Manuals Beat The Water Industry's Brain Drain?
By Ken Schnaars and Chris Somerlot
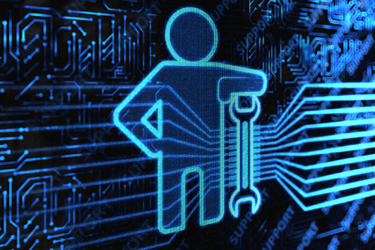
Water industry brain drain is here. As of last year, half of U.S. adults aged 55 or older had retired, according to Pew Research Center. Furthermore, by 2030, the Water Environment Federation predicts that a third of the water workforce will be retirement eligible.
This means decades of operations and maintenance (O&M) experience and expertise is also going with them.
To stop the O&M exodus and build a more resilient knowledge base, some utilities are turning to electronic operations and maintenance (eOM) manuals as a solution. eOM manuals can capture and retain institutional knowledge and help utilities optimize their operations and build resiliency. As part of an effective utility management strategy, eOM manuals can measure a utility in a comprehensive way that aligns with its long-term plan.
“People may come and go,” said Ken Schnaars, Brown and Caldwell Senior O&M Consultant, “and knowledge fades. The industry needs a better solution than paper manuals to capture this knowledge and grow from it.”
With support from America’s Water Sector Workforce Initiative, the federal program that aims to recruit and retain the next generation of water workers, there is ample opportunity for utilities to advance investment while reducing costs. Indeed, in Bluefield Research’s “Forecasting Municipal Operating Expenditures in a Post-COVID World, 2021-2030” report, one of the fastest growing operating expenditures for water utilities is software and digital technology.
Benefits
Already, many utilities have a library of O&M manuals from a wide variety of projects, consultants, and deliverables, but what is lacking is the ability to put all of these projects together into a working system and understand how all of the equipment works together. That’s what an eOM manual can do. It is a living document that puts information at your fingertips from multiple sources.
“One of the advantages of having an electronic O&M is the power of search to get through a lot of content,” Brown and Caldwell Project Engineer Chris Somerlot said. “When someone searches for something like a well, you get a list of results within that eOM, like an operator log or a video. When you go to that video, it also transcribes it for you and even that transcription is searchable.”
Plus, eOM manuals can:
- Reduce mistakes
- Improve response times
- Expedite maintenance and access to O&M information
- Meet state regulatory requirements
“I go to so many facilities and I ask things like, ‘Where does this pump go?’ or ‘What is the high-pressure limit in which this shuts off?’ and O&M staff have no idea,” Schnaars explained. “We have to search the file cabinets and a bunch of other information because it’s not readily available. eOM manuals bring that together.”
eOM manuals also set up utilities for advances in technology.
“One of the cool things is that new features come along all the time, such as using your mobile device,” Somerlot added. “You can integrate things like your GPS location and camera to enable an easier workflow.”
For example, staff can tag a piece of equipment such as a valve with a QR code, making its related data easy to access with a remote device, i.e., a mobile phone. Once scanned, the QR code could take the user directly to that valve’s page in the eOM manual, providing a shortcut to information, such as maintenance history, process theory, lockout/tagout, and daily log.
Knowledge Is Power
While the benefits are clear, Somerlot said an optimized eOM manual takes it even further. An optimized eOM manual also converts a utility’s knowledgebase into easily updatable formats that are not only highly accessible, but also offer real-time feedback of system operations and built-in tools to identify the gap between inefficient processes and optimal performance.
In addition to data and technology, equally important are the people and adoption.
“Brown and Caldwell’s approach to optimization, BC:Opta, is built upon three components — people + technology + adoption,” Somerlot added. This achieves immediate and long-term impacts and improved planning and performance. The people part is having the right subject matter experts. The adoption comes from fostering a collaborative environment where key stakeholders feel empowered and invested in the new system’s success.”
The Future
With an optimized electronic format, O&M manual content possibilities are limitless. On the horizon are real-time dashboard integration and training materials, such as videos, PowerPoint, even quizzes. That coupled with an effective utility management strategy, eOM manuals can help build a more resilient knowledgebase to fight brain drain and help measure utilities in a comprehensive way that helps them achieve their long-term goals.
As Somerlot pointed out: “It’s always about the content and how you can easily get it to the people who need it when they need it most.”
Ken Schnaars is a Brown and Caldwell senior O&M consultant. A certified wastewater treatment plant operator and licensed professional engineer, Ken is an operations and maintenance expert with over 45 years of specialized civil environmental engineering experience.
Chris Somerlot is a Brown and Caldwell project engineer. He has nearly 20 years of experience in engineering, information technology, and software development.