Halogen Stabilization As An Efficient Biocidal Treatment Program In Wet-End Papermaking Applications
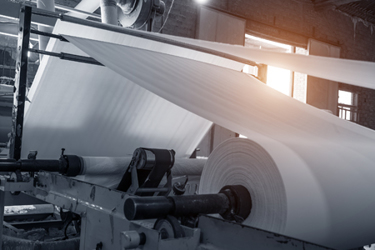
The proper selection and use of wet-end biocidal treatments is a key element in the effort to optimize efficacy and efficiency in papermaking. Biofilm control represents a particularly challenging form of microbial control in a paper mill and can lead to a variety of mechanical and final product issues. Chlorine-based biocides are often selected to maintain microbial control due to cost, efficacy, and ease of application considerations. Hydantoin stabilization technology was developed to benefit from the advantages of chlorine-based oxidants while improving efficacy, efficiency, and potentially overall cost of the treatment program.
The Need For Biofilm Control In Papermaking
Any factors that risk downtime to operations or disruption of sensitive chemical processes in continuous papermaking production lines can be costly in terms of lost productivity or detrimental effects on product quality. It is imperative to discourage biofilm growth that can foul equipment surfaces, create hazardous working conditions, contaminate paper products, or produce visible stains that compromise product quality. Biofilm control is only one part of the story. It is also important to optimize that control without incurring additional financial and operational problems in the process.
Considerations In Biofilm Control Options
Papermaking operations can use a variety of products to control biological contaminants that could cause biofouling on process equipment and in the final product. Chlorine-based biocides are often selected to maintain microbial control due to cost, efficacy, and ease-of-application considerations, but there are also limitations. Because chlorine reacts with all organics, its chemical effects do not stop with its desirable activity on biocidal activity. Without mitigation, this can lead to problematic cost impacts for multiple aspects of operation, corrosion of equipment, and cosmetic flaws on paper products.
Fortunately, the availability of halogen stabilizers that can maintain the desirable characteristics of chlorine-based biofilm control and removal — while minimizing undesirable side effects — offers better options across multiple areas of concern.
- Cost Concerns. Stabilizing chlorine activity can deliver operational savings in several areas. First, by extending the longevity of chlorine activity, a stabilizer can encourage good biofilm control with an estimated 30 percent reduction in hypochlorite consumption. This reduces bleach costs, reduces the formation of adsorbable organic halides (AOX), and reduces the risk of compromising papermaking additives (e.g., polymers, polyacrylates, phosphonates, etc.), which are susceptible to chlorine attack.
- Operational Concerns. Because it is difficult for chlorine to penetrate biofilm, additional chemical additives are used to improve its activity. A stabilizer that better controls the reactivity of chlorine will allow the stabilized halogen to penetrate deeper into the layer of biofilm (Figure 1).
It can also reduce the potential for oxidizing organic papermaking additives such as optical brighteners, retention aids, or wet- and dry-strength aids, thereby minimizing the need to overdose those costly chemicals. Also, using a stabilizing additive that can be premixed with hypochlorite to provide long-lasting activity can require only one dosing point, as opposed to other systems requiring multiple dosing points.
Figure 1. The ability of a stabilized hypochlorite mix (left) to penetrate deeper into the biofilm layer can provide better overall control than more aggressive treatments (right) that quickly use all of their oxidizing action on the surface layer of the biofilm and on other organic compounds in the water.
- Concerns. Cleanliness of papermaking machines is an important aspect of quality control (QC), especially in fine paper production. In addition to fouling production equipment surfaces, slime formation can also impact product quality. Drips of slime can break through the newly formed fiber mat or paper web near the wet end of the papermaking machine (resulting in costly, disruptive shutdowns) or can discolor the finished product (increasing costly waste and QC interventions).
- Environmental Concerns. As a byproduct of effective biofilm control, chlorine can also create undesirable disinfection byproducts (DBPs). Using a stabilizer that reduces the volume of hypochlorite required and stabilizes the molecule can help to minimize DBP formation and improve safety. Maintaining the delicate balance between maximizing biofilm control and minimizing chemical use also helps to sustain water reuse efforts and manage the true cost of water, which gets magnified during periods of water scarcity. And for ecologically minded paperboard manufacturers that use significant amounts of recycled paper, getting better bioactivity helps them deal with the increased contamination that recycled paper adds, even while reducing chemical use and water demand.
The Best Of Both Worlds
Drawing upon decades of experience in biocide treatment and halogen stabilization, Sigura™ developed Equinox® Stabilizer, a DMH-based (5, 5-dimethylhydantoin) halogen stabilizer to optimize halogen availability in papermaking operations. This solution enables paper and paperboard producers to get the best of both worlds — an increased biocidal efficacy of chlorine (Figure 2), with minimal negative side effects such as corrosion and interference with other chemical additives.
In addition, Equinox® Stabilizer is considered non-hazardous and does not require special handling procedures or licenses.
When used in combination with hypochlorite, Equinox® Stabilizer offers multiple benefits:
- Optimizes the availability of active halogen for penetration of biofilm.
- Reduces bleach consumption.
- Reduces potential for equipment corrosion.
- Is compatible with other chemical treatment additives.
- Is non-hazardous and environmentally friendly (reduces AOX in discharge water).
Graphic courtesy of Sigura
Figure 2. Results from a comparative study show that a 5-ppm concentration of sodium hypochlorite treated with Equinox® Stabilizer reduced biofilm growth by 90%.
Learn how bio-control in paper & board production should be the center of your water treatment program by attending our free webinar presented by Lievin De Vriese, Business Development Manager at Sigura. Secure your spot.