Automatic Delivery Gives Back: A Hard-Water Case Study
By Julia Selwyn
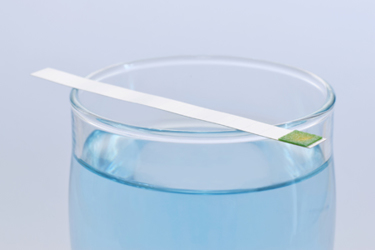
Eighty-five percent of the U.S. has hard water, characterized by a high concentration of calcium and magnesium ions.1 This means 85% of the nation’s population must use more time and cleaning solution to achieve the same results the other 15% have no trouble with. From hand-washing to laundry, hard water takes its toll in more ways than one. Dry skin, cloudy dishes, and higher maintenance on industrial appliances are just a few of the many effects hard water has.
On a more serious note, “Several epidemiological investigations have demonstrated the relation between [hard water and] risk for…cardiovascular problems, diabetes…neural diseases, and renal function.”2 Water softening systems are often the solution to mitigating these concerning potential effects but neglecting to regularly feed the system with water conditioning salt can resurface these issues in no time.
It was vital for the company in the following case study to provide soft water to their residential and care community as not to have their water supply be the cause of any negative reactions amongst their residents, guests, and employees. But laboring to handle the numerous amounts of salt bags needed to keep the system running properly would become too much of a physical health risk to place upon facility workers. This would mean that in protecting their community’s health with softened water, they would be asking facility workers to expense their own and do the back-breaking work to manually feed the softeners. They were in desperate need for “game changing innovations, profitable solutions and new ideas to maintain their competitive edge.”3 Find out what they did to meet the challenge and exceed their goal in the process.
Situation
A national corporation planning the construction of a new residential housing and care community in a hard water area was seeking the most efficient method of providing soft water to the entire community. An analysis of prior operations revealed many cost saving opportunities if they installed a central water conditioning facility. They determined that the cost of softening the water for all the facilities would eliminate the high cost of man-hours required to deliver small quantities of salt to the individual cottages, as well as, apartments, commons area, and special care facilities.
Challenge
- Design a central water conditioning system.
- Provide for ample water supply for fire suppression.
- Size the softeners to allow for community growth.
- Provide cost savings, risk management, and reduce environmental impact.
- Eliminate the storage space needed for a large number of salt pallets.
Solution
The project manager worked with an engineering firm to design a central water conditioning system to provide softened water to the community. This was accomplished by constructing a water softener vault to house the softener bank. To meet local codes, a bypass was installed on the water main supplying the softeners to ensure adequate water for fire suppression. The engineering firm collaborated with the softener manufacturer along with an industrial and commercial salt supplier to provide the salt need to feed to the water softener. Once the softeners were sized, the salt supplier provided the proper size automatic brine delivery system. A central softener and the brine system allowed for the elimination of handling bagged salt, and it was more cost effective than installing and maintaining softeners at each of the 140 locations where soft water was required.
Results
- > $15,000 Operations Cost Savings Annually
- > 16,000 lbs. Carbon Footprint reduction to date
- Elimination of need for 1,200 sq. ft. receiving and storage space, resulting in a savings of $300,000
- $25,000 salt handling equipment savings
Therefore, while softened water reduces the effects of hard water, automation is the key to ensuring the water’s regeneration process is never interrupted. This allows facility workers to focus on other aspects of the community’s operations, knowing that the automatic brine system does the work on their behalf.4 As a result, residents, guests, and employees can always enjoy water at its optimal quality and trust appliances throughout the campus are achieving operational efficiency.
When it comes to establishing communities with high functioning facilities, the water supply shouldn’t be a negative weight on the people who are there. In other words, having quality water should not be dependent upon whether or not facility workers risk their own health for it by regularly accessing tight mechanical spaces with salt bags. Water should not be why people leave a job or residence when automation can make it the reason they keep coming back.
By introducing automation at the drawing board of communities like these, engineers can work with facility owners and brine system suppliers to design a process that benefits everyone. Salt storage becomes unnecessary and logistical problems relating to manually hauling salt bags are a thing of the past. Automation offers a solution to water supply and brine delivery other methods simply fall short of, while continuing to challenge the traditional ways hard water is approached.
Julia Selwyn is the Marketing and Sales Administrator of AUTOBrine®, a customized brine delivery system that automatically provides brine to water conditioning equipment where normally, manually loaded salt bags for the regeneration process would be required.
References