ALCO Waste Management Case study
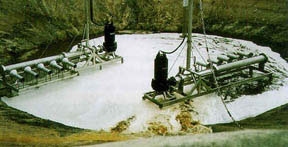
In the past, landfill was just that—dig a hole and fill it with waste. However, this approach is known to cause long-term environmental problems through the production of greenhouse gases, such as carbon dioxide and methane, which are given off as the waste degrades, and potentially polluting leachate carried by rain into the ground water.
It is now recognized best practice to manage landfill sites according to strict environmental guidelines relating to the use of impermeable liners, either natural or man-made, and active leachate and landfill gas extraction systems.
One such managed site is owned and operated by ALCO Waste Management at
Workington, United Kingdom, just to the west of the Lake District National
Park.
The site is a co-disposal site, handling a wide range of solid and liquid industrial wastes. The site has a natural clay lining which is reworked and tested to ensure that it meets or exceeds the impermeability standards required for landfill site liners. Leachates collect in the basal drainage system and landfill gases are extracted to a flare unit. The leachates are pumped out to a lagoon, where they are oxygenated in an activated sludge basin to break down the pollutants.
The strength and volume of the leachate meant that the existing conventional aeration system was becoming overloaded. Foam and aerosol formation was also becoming a problem on-site. The chemical oxygen demand ranged up to 85,000 parts per million, with fluctuation in the volumes of leachate requiring treatment.
One considered solution to this problem was to build additional aeration lagoons, an inefficient and expensive use of the landfill site. This would also serve to exacerbate the foam and aerosol problem and could also lead to odor generation on-site through the excessive contaminated gas release inherent with traditional aerobic systems. After discussions with ALCO Waste Management, Andy Tassell of Air Products plc proposed that the treatment capacity of the plant could be increased by increasing the quantity and quality of biomass in the lagoon, through the use of pure oxygen.
An Air Products Oxy-Dep™system was installed which dissolves pure oxygen into the effluent at the rate of 4 tonnes per day. This increases microbial activity, ensuring that the COD of the effluent complied with the consent level of 5,000 parts per million. Conversion to pure oxygen significantly reduced volatile emissions from the lagoon surface, resolving foaming, mist and potential odor problems at a stroke. The improvement in the process treats the leachate to within consent levels, avoiding the need for new lagoons.
Such was the success of the installation, ALCO Waste Management Ltd are now installing a larger, purpose-built treatment tank to cope with the potential increase in leachate production from their new landfill extension and development of their chemical treatment plant.
Air Products and Chemicals, Inc., 7201 Hamilton Boulevard, Allentown, PA 18195-1501. Tel: 610-481-4911; Fax: 800-880-5204.