A Unique Approach To Dewatering Sludge Overcomes Problems Of Conventional Methods While Saving Money
The key to the process is its "dewatering drum" that can achieve both thickening and pressing (dewatering) of the sludge in a single, compact operation. It enables the Volute Dehydrator to take sludge as dilute as 0.1% solids directly from a biological process, such as an oxidation ditch, and produce cake of over 25% solids. Separate thickening, storage, and conditioning processes are eliminated. In addition, the need for operators, continuous use of wash water, high noise, and high power consumption are eliminated—all of which reduces expense.
Unique Dewatering Drum Design
Spacers and fixed rings are held in place on four rods. Moving rings, slightly smaller than the outside diameter of the screw and slightly narrower than the spacers, are located between the fixed rings and are moved by the screw. The initial section is the thickening zone from which the filtrate is discharged. The pitch of the screw narrows and the gaps between the rings decreases toward the end-plate where solids are discharged. Pressing of the sludge occurs here.
Fully Automated, Requires Little Operator Attention
Sludge is fed into the sludge service tank where it may be dosed with a coagulant, if necessary. From here, the sludge is fed into a flow control tank and on to a flocculation tank, where polymer is added. After a short residence time, the flocculated sludge overflows into the dewatering drum where it is pressed. The Volute Dehydrator controls the entire operating sequence, including sludge feed controls, polymer makeup, and dosing.
Fully automated, the Volute Dehydrator controls the operation of wasting sludge directly from the biological process or clarifier, chemical make-up and dosing, flocculation, and then dewatering. Other than periodic inspection and chemical replenishment, the Volute Dehydrator requires very little operator attention. In fact, depending on operating conditions, a partial overhaul of the dewatering drums may be required only every three to six years—a half-day operation done on-site with negligible disruption to the operation of the wastewater treatment plant.
Advantages Add Up to Reduced Expense, Superior Performance
- No thickeners, sludge storage, or separate dosing facilities required
- No regular operator attendance required
- Produces high-quality filtrate that does not need to return to the head of the process (i.e., high solids recovery)
- Low noise and odor
- Low power and wash water consumption
- Able to handle oily sludge
- Flexible—can handle feed sludge from <0.2% to >4%
- Rapid installation
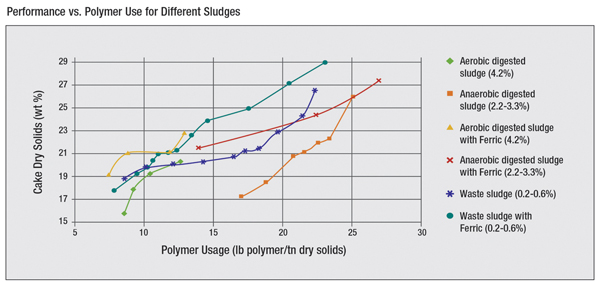
Sludge Type | Feed
Concentration (%) |
Cake Solids (%) |
Solids
Recovery (%) |
Polymer Use (lb/t dry solids) |
Max.
Throughput (lb dry solids/hr/dewatering drum) |
Aerobically Digested | 4 | 18 - 25 | 98 | 7 - 12 | 75 |
Anaerobically Digested | 2 - 4.4 | 18 - 27 | 99.5 | 10 - 25 | 65 |
Waste Activated | 0.2 - 0.8 | 20 - 29 | 10 - 22 | 10 - 22 | 35 |