A Simple Solution To DBPs, Color Issues, And Membrane Fouling

By Kevin Westerling,
@KevinOnWater
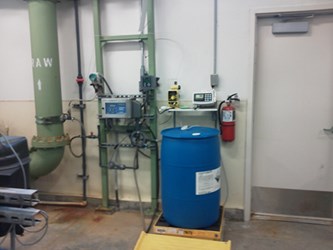
Faced with escalating O&M and regulatory concerns due to membrane fouling, a Colorado drinking water facility discovered the key to success: chemical control.
Even the most advanced drinking water treatment systems can have drawbacks and complications. Microfiltration certainly falls under the definition of advanced — the Grand County Water and Sanitation District was the first facility in Colorado to adopt membrane filtration — but membranes only work well when they’re clean. And while Grand County’s setting is pristine, nestled in the Rockies with source water from the Colorado River, its membranes certainly were not.
Aluminum chlorohydrate, a polymer flocculant used to manage color spikes attributable to leaves and debris from the springtime thaw, was stubbornly sticking to the membranes. The impaired treatment due to fouling put the municipality at risk for regulatory violations and a possible downgrade of its 1.5-MGD rated capacity. Compliance with the U.S. EPA’s Long Term 2 Enhanced Surface Water Treatment Rule (LT2SWTR) and Stage 2 Disinfection Byproducts Rule (DBPR) were of concern, but Grand County also remained steadfastly committed to keeping the water crystal clear for its residents and visiting skiers. Either something had to give, or a new solution would have to be found.
Swing-And-Miss Fix
The first and typical reaction to fouled membranes is to clean them more often and vigorously. That logical approach, however, was ineffective in this case.
“The polymer was sticking like it was painted right onto the membranes,” said Kris Bassett, Grand County’s ORC (operator in responsible charge). “We just couldn’t get them cleaned up, and we had to go to a harsher chemical.
“We would have to do these day-long chemical cleans, where the water is heated to 34 degrees Celsius before you add your cleaning solution. Our water is so cold that we would have to wait six to eight hours for it to get up to that temperature. We couldn't do that every week, which is what it was calling for with the membranes so plugged off.”
Besides the O&M headache, the aluminum chlorohydrate was negatively affecting pH, which had fallen from the ideal range of 7.4 to 7.6 down to about 6.6. To get to the proper pH level where the flocculant works effectively and doesn’t stick to the membranes, caustic soda needed to be added. According to Bassett, the whole process amounted to a guessing game.
Microfiltration units at the Grand County Water and Sanitation District
Gaining Control
Bassett and Grand County’s two other crew members, consisting of a fellow operator and the plant manager, were relatively sure they had the right answer to their problems — using coagulant to resolve color and chemical cleaning to reduce fouling — but were simply wrong on dosing and timing. Luckily, as a 26-year veteran in the industry, Bassett knew where to turn for a solution.
In fact, he was a key part in the development of the solution — a technology that now goes by the name Clearlogx and is marketed by Siemens. Back in 2006, just after Grand County had upgraded from mixed media filtration to ultrafiltration, the Clearlogx technology was in its infancy. Bassett had worked alongside a consultant on a control system that would analyze, optimize, and deliver chemical dosing. Grand County seemed like the ideal testing ground for the nascent system, so it became the site of a full-fledged pilot study.
Startup, Operation, And Performance
Installation required minimal labor, and even less space. The Grand County pilot system includes a streaming current monitor and a pH monitor — each measuring less than a single square foot — and the main control panel measuring 2½ square feet x 8 inches deep. The panel can be set up and operated from anywhere, needing only wiring to connect to the monitors and metering pumps. It can also be easily programmed for integration into a utility’s SCADA system, which is what Grand County did.
Kris Bassett stands beside the Clearlogx control panel.
Once hooked up, the system figured out that Grand County was using more aluminum chlorohydrate flocculant than was necessary for coagulation and color removal. Less flocculant resulted in far less fouling and chemical cleans, thereby increasing performance and reducing O&M. The system also steadied pH by increasing the caustic feed. With pH at the optimum level for microfiltration, Grand County was able to reduce chlorine and total organic carbon (TOC) — precursors to highly regulated disinfection byproducts (DBPs).
“We were always just real close to the edge of DBP compliance and we thought, ‘Well, either they're going to change the standards or we’re going to start going over.’ When we put this in place, the DBP numbers immediately backed off,” remembers Bassett.
Correcting the pH also helped with corrosion control. “I think the recommendation is that water hardness be no higher than 90 ppm [as calcium carbonate equivalent] to prevent corrosion,” said Bassett. “We're at 20 ppm or less. Our water is so clean — we just don't have anything in it.”
Cost And Payback
Capital costs for the system were recovered relatively quickly through O&M savings, according to Bassett.
“The year before we had it, we invested so much extra in cleaning chemicals, electricity for heating the water, and man-hours during clean-in-place runs. It was getting to where somebody had to be there all the time, almost.
“With the automated feeder in place, we've cut way back to where maintenance on the membranes should be, to what we would call normal operation. We can have maybe 500 hours of runtime before doing a clean-in-place; we were only getting maybe 30 hours of runtime before. You start figuring that out, it saved us a huge amount.”
Chemical feed under control: an inconspicuous but effective solution
The only maintenance required now is intermittent cleaning of the pH probe, as well as cleaning and replacement diaphragms for the metering pumps — “just what you would have to do anyway,” said Bassett. “Really, as far as the system itself, there's almost no maintenance to it.”
With only three full-time employees serving a community that peaks at about 3,500 customers during “busy” season, Grand County is the definition of a small operation. The utility could ill-afford wasted resources, so seeking out automation was a wise decision. The efficiency gains they realized, however, are even more pronounced with larger systems, for which Clearlogx is also compatible. As Bassett put it, “When you start getting into tank cars full of chemicals and you have that kind of control, you can save a huge amount of money.”
It’s all about improving the bottom line. And the bottom line is, when it comes to precision, machines just do it better.