A Bridge Over Troubled Water: The Journey To Serialization Compliance
By Nicolas Girard, Ropack Pharma Solutions and Graham Clark, TraceLink
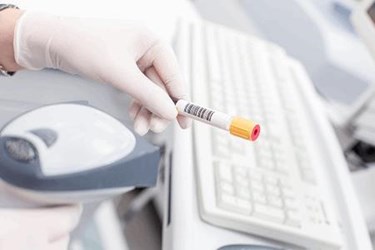
access the Article!
Log In
Get unlimited access to:
Trend and Thought Leadership Articles
Case Studies & White Papers
Extensive Product Database
Members-Only Premium Content
Welcome Back! Please Log In to Continue.
X
Enter your credentials below to log in. Not yet a member of Water Online? Subscribe today.
Subscribe to Water Online
X
Subscribe to Water Online