ABOUT HOMA PUMP TECHNOLOGY
Headquartered in Ansonia Connecticut, we have been serving the North American wastewater industry quickly and reliably for 35 years through our network of competent and locally committed factory trained distributors and service centers. Our 40,000 sq. ft. engineering & test center, workshop, and warehouse facility is fully equipped to help design, build, deliver, and service all your wastewater handling needs. Our dedicated and competent staff provides full support; from applications and product selection, to the initial purchase and installation of your equipment, planned maintenance, spare parts sales, replacements and upgrades. For more complex projects and custom product solutions, our German Manufacturing and Technology Center’s electrical, mechanical and hydraulic experts are standing by to assist and innovate.
Downtime is a dirty word, so we specialize in fast deliveries from our over $10M pump and spare parts inventory. 5-7 days is standard for submersible pumps up to 120 HP, with same day delivery possible for emergencies. Retrofit with HOMA, or let us support you with an engineered new installation. HOMA builds submersibles that work. Simple. Reliable. Efficient.
Products
- Submersible motors from 1 HP to 500 HP
- FM Class 1, Division 1, Groups C&D
- Jacketed Motors from 2.8HP for Wet or Dry pit installation
- Submersible Wastewater pumps with channel impellers up to 8“ solid size
- Heads to 275' tdh, flows to 20,000 gpm
- Submersible Axial flow propeller pumps
- 5,000 to 35,000 gpm
- Full range of submersible Grinder pumps to 15HP
- Standard CI material is ASTM A48 Class 40B
- Submersible Stainless Steel Pumps
- Submersible mixers
- Non-proprietary abrasion resistant silicon-carbide seals
- Complete line of adapter brackets for direct replacement of other pump brands.
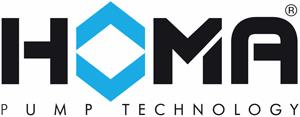
CONTACT INFORMATION
HOMA Pump Technology
390 Birmingham Blvd.
Ansonia, CT 06401
UNITED STATES
Phone: 203-736-8890
Fax: 203-736-8899
Contact: Anna Houley
FEATURED CONTENT
-
In this episode of Water Talk, Angela Godwin sits down with Nick Terranova from Homa Pump Technology to talk about decreasing lifecycle costs by focusing on lifecycle efficiency.
-
Operating high, and to the left of the performance curve requires a pump designed to handle that sort of application.
-
In this episode of Water Talk, Nick Terranova from HOMA Pump Technology discusses how the water industry has changed, and how it will continue to change in the coming years.
-
This article explores some of the best practices to ensure overall station reliability, i.e., “total station efficiency,” in order to keep operating costs and downtime at a minimum.
-
Jim Torony, President of HOMA Pump Technology, recently sat down with the Water Online editorial team to talk about all things HOMA, their pump technology and shared his thoughts on the water industry as a whole.
-
When selecting a submersible pump model, the question may arise of what type of impeller is best for the application. We will examine the pros and cons of these styles, as well as common materials of construction.
-
An overheating pump motor can be a worrying issue for operators and engineers alike, but like many pump issues, it is usually a symptom that can be traced to a problem in the system. These common causes of motor overheating are good places to begin.
-
Emmons Metro asked HOMA to provide a solution to a critical station at a facility that handles wastewater from produce and associated packaging for a large supermarket chain in the Northeast.
-
Variable speed pumping using a variable frequency drive (VFD) can be a powerful tool in a pump system. Incorrect application can do more harm than good. Here’s how.
-
Utilities, consulting engineers, and OEMs concerned about protecting low-horsepower pumps against overheating in ‘dry-pit’ (non-submerged pump) applications appreciate new designs that can negate historic problems prone to cause excessive pump maintenance or premature replacement. While all submersible pumps rely primarily on the pumped fluid for cooling, certain designs can better tolerate today’s debris-laden wastewater to keep processes flowing without costly workarounds. Here’s how.
-
In addition to all the challenges of responding to the biological demands of wastewater treatment, packaged wastewater treatment plants — aka, package plants — also face physical and financial demands related to size and efficiency. Here are several factors that can help utilities, design engineers, and package plant OEMs reduce cooling concerns and maintenance costs when using low-hp pumps (<10 hp) in open air applications.
-
Every pump retrofit installation faces different challenges. That is why looking beyond specified flow rates alone can pay dividends many times over in correcting historical problems and improving operational efficiency.
-
A common misconception when a pump goes down in wastewater applications is that the pump is always the source of the problem. The reality is that many — if not most — failures occur because of the system’s impact on the pump or because of other external environmental/operational factors.
-
Pump clogs cause sanitary sewer overflows (SSOs) and backed up lift stations that damage the environment. They also put the public health at risk and lead to regulatory fines for the utility.
-
Wastewater lift stations collect every type of debris. From wipes to t-shirts, from rocks to boards, some strange materials end up in the wet well. Unfortunately, some of these items don’t make it through the pump. Many operators have spent Super Bowl Sunday pulling a clogged pump to remove stringy rag balls or other debris. And in severe cases, sanitary sewer overflows result in regulatory fines.
-
Reliable operation and energy efficiency are both of paramount importance in wastewater pumping. Reliable clog free operation has always been the strength of HOMA heavy duty wastewater pumps - but we have now combined the next generation higher performance wet ends with our new IE3 premium efficiency motor to create the “EffTec Solution”, the latest HOMA innovation. Watch the video to learn more.