Proactive Chemical Mitigation System Enhances Public Safety For Chlorine Disinfection Operations
By Cliff Lebowitz
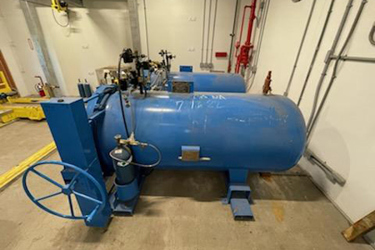
City Takes Advantage Of Secondary Containment Vessels For Chlorine Gas Cylinders, With Only Minimal O&M Additions
A public works maintenance manager, with responsibilities including multi-site water treatment, credits a proactive chemical mitigation system for enhancing public safety at chlorine disinfection sites that typically operate proximate to exposed populations.
In addition, with maintenance staff limited while covering a variety of public works responsibilities, he also credits minimal added maintenance burden deriving from the units, as well as noting that operators have found them easy to work on and understand.
“When you’re reactive (instead of proactive), that’s when people get hurt,” summarized Wil Tomplait, a public works maintenance section chief for the City of Houston, in an interview with the manufacturer of the units.
Among other public works responsibilities, he is responsible for installation, maintenance, and repair for over 60 chlorinator-based, chlorine disinfection sites within the city and surrounding areas, which sometimes also include ammoniators for delivering LAS for control of disinfection byproducts (DBPs) that derive from the chlorine use.
“The majority of our sites are in high-risk areas,” he continued, “such as being close to an apartment complex or a public park, or just busy areas. Among the four sites where we have (the secondary containment vessels), one is across from a prestigious park, and another is around houses where there is only a chain link fence (around our facility). There is imminent chance of public exposure, and we have the confidence that if anything happened it would be contained.”
Tomplait added that the pro-active containment for any leaks helped the utility take advantage of chlorine gas as a preferred alternative to disinfection using liquid chlorine.
“Gas gives us quicker disinfection time and shorter detention times,” he noted. “Those systems are easier to manage; relatively small, and easier to work on. Also, we don’t have to worry about a (gas) release when the secondary containment vessels are in place. When it happened once, it was all contained, so we just hooked up our vacuum feed system (to the containment vessel); and when all the gas was evacuated, we went in and replaced the cylinder.”
The secondary containment vessels for chlorine gas cylinders are manufactured by TGO/ChlorTainer of Santa Rosa, CA. They note that the vessels can provide safety containment not only for chlorine gas, but also for sulfur dioxide and anhydrous ammonia.
Asked about the product performance, Tomplait noted that the secondary containment vessels had performed well, with assistance readily available from the manufacturer as needed, including multiple site visits.
“We haven’t had any issues,” he said. “The units are relatively easy to work on, and TGO has been extremely helpful whenever I’ve needed it. The plant operators check on the chlorinator operations every day — (including) chemical feed (rates), replacing cylinders, making sure everything is working. Where they (containment vessels) are, we haven’t had any issues. They have always performed well and done their job. I appreciate the structure and engineering that goes into that; it makes our job a lot easier.”
“The operators are very comfortable with (the functioning of) the units, which they found easy to grasp and understand. Being new to water plant operations, I had some trepidation myself when I first saw them, but now know it’s cut and dry to use them. You just load (the cylinder) in, make sure the door is closed, and let it ride.”
“They are pretty easy to maintain; it’s very simple and straightforward,” he continued. “You can easily see if anything needs to be done, they don’t take much time, and we usually don’t need help. But due to time constraints on our staff here, with many sites to take care of, we might look into working with an (independent) contractor the manufacturer knows, to take care of annual maintenance for us.”
“Our operators get training from multiple sources for chemical operations. They get it from more senior operators and from myself, and when I don’t have the time, we have senior mechanics staff to help with the ins and outs.”
“You can never be too safe around chlorine gas. (Regarding the secondary containment vessels) I would not hesitate to recommend them as part of a risk management program, and especially where space is (too) limited (for considering alternative measures to protect exposed populations).”
In a third-party report last year, engineering and operations management in drinking water operations for the city stated that plant operators have been “buying in better” on the use of secondary containment vessels as a reliable, lower-maintenance, enhanced leak safety alternative to wet and dry scrubber systems. In particular, they credited enhanced storage building design and secondary containment system innovation as helping considerably in the improved operator buy-in.
Previously, in a 2021 article, their consulting engineering firm had noted “significant savings in maintenance and insurance costs” by being able to “decommission a scrubber system and its associated appurtenances.” In any event, operators also noted a new benefit of capturing leaked chlorine for re-injection, rather than “losing it” through scrubbers.
Sandeep Aggarwal, PE, the manager of the groundwater facilities group within Houston’s drinking water operations, noted that despite some reliability problems with scrubbers, such as occasional, readily handled, brief outages due to electronic control issues, concerns with the presence of caustic media with wet scrubbers, and sparking potential with dry scrubbers, the utility was committed to continuing to confidently deploy that technology for leak safety in various installations and facilities, while noting significant advantage deriving from use of the alternative secondary containment vessels.
“We were pleased to learn about this technology at a water conference and have noted significant reliability and maintenance advantages through its use as an alternative to scrubbers,” he said. “For example, when a 1970s era scrubber had ended its useful life, we deployed this technology as an alternative to a new scrubber, and found it more reliable and easier to maintain, without incurring higher capital cost.”
In an email, Rudy Caparros, Chief Operating Officer for Chlortainer/TGO Technologies, Inc., explained the fundamental proactive nature of the company’s product.
“With any accidental releases of chlorine gas within the vessel, everything goes into process,” he stated. “There is no waste. Since all the gas is contained and put into process, there is no need to report a release, but even more importantly, an operator never has to respond to a hazmat situation.”
Cliff Lebowitz (cliff@catalyticreporting.com) is Principal and Editorial Director at Catalytic Reporting, LLC. His third-party case histories, usually industrial equipment applications, are based on interviews with end users and their engineering firms, and are approved by them for accuracy and completeness. He holds a BS in Biology from Rutgers University.