New Membrane Technology Challenges Tradition To Better Handle Harsh Metal Wastewater Streams
By Greg Newbloom
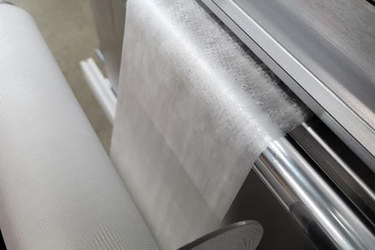
New electronic devices, electric vehicles (EVs), or other cool technologies bring us delightful conveniences, but they also induce some headaches. Metal wastewater streams, a byproduct of the manufacturing processes of microelectronics, EVs, and a whole host of other industrial processes, are no different and pose their own challenges.
A Legacy Of Issues
For decades, manufacturers have embraced several methods for dealing with metal wastewater, but many of those methods contribute to significant carbon emissions and rely heavily on labor, chemicals, and third-party services. Sorting out how to run these processes sustainably, reliably, and on budget can bring a headache to even the most careful industrial facility manager.
Metal wastewater streams cannot be simply sent to sewers because there are environmental discharge limits designed to protect the public. Traditional treatment and disposal options for these streams are limited and have not evolved to current environmental regulations or sustainability expectations. Thankfully, emerging companies are guiding industrial clients through a new approach, from analysis to resolution.
Here are some of the legacy approaches:
Concentrated metal streams that are highly acidic and toxic — including copper, nickel, and arsenic — are trucked offsite for disposal and/or incineration at a remote location, which costs facilities hundreds of thousands of dollars per year. More dilute metal streams, also highly acidic, are typically treated with single-use conventional selective ion exchange resins or are chemically precipitated into a toxic sludge. The concentration of metals in wastewater dictates how often the resins will require replacement with fresh resin beds or how often sludge is dewatered, depending on the process being used. Metal sludge and exhausted resin beds are both trucked offsite for either disposal or further processing for potential reuse. These processes are expensive and result in massive operational costs each year.
Introducing ECD
There is a strong new alternative to trucking wastewater and the other legacy approaches. Electro-ceramic desalination (ECD) membranes excel in highly acidic and oxidizing wastewater streams, thanks to their amorphous silica structure. These membranes not only provide significant advantages in treating challenging streams but also offer cost savings by reducing the trucking of wastewater offsite, reducing chemical and labor from sludge processing, or by extending the useful life of conventional ion exchange beds.
New ECD processes treat concentrated metal wastewater streams with recovery rates up to 98%. These processes reduce problematic metals into a much lower volume brine waste. This waste can either be trucked off site or can be further treated via electrowinning process to extract the concentrated metal from the ECD brine. In this case, that means eliminating the need for trucking off any waste. The ECD product water either meets the sewer discharge limits or can be re-used in other areas of the facility, such as cooling towers.
Electro-ceramic desalination membranes are also used to reduce the contaminant loading onto conventional single-use ion exchange (IX) resin beds, which are typically used to treat dilute metal wastewater streams. An ECD system is installed as a pretreatment step and removes the bulk of the dissolved metals from the wastewater before it enters the conventional IX beds. This process addition greatly reduces the frequency, sometimes 10x less, the IX beds must be replaced after exhaustion. In some cases, ECD product water meets the metal discharge limits and hence eliminates the need for a polishing step by conventional IX beds all together. The concentrated brine from the ECD system is typically routed to be blended with the concentrated metal wastewater stream.
Pilots And ROI
Incorporating electro-ceramic IX technology to treat those challenging wastewater streams typically yields return on investment to customers in less than two years. In some cases, the ROI is less than a year. Consider an EV battery manufacturer with a lithium (Li) wastewater stream that is currently being trucked offsite. After conducting a pilot study, one electro-ceramic membrane was able to reduce the volume of trucking by 92% and reduced the concentration of Li by 90-92%, delivering an ROI of less than 13 months.
A different pilot study yielded a customer with a concentrated copper (Cu) stream that was currently being trucked offsite towards a reduction of trucking volume by 80% and Cu concentration reduction by 99%, which would give an ROI of less than two years.
Legacy approaches to metal wastewater can now be reconsidered and discarded. Integrations of the new technology into existing industrial processes have been accomplished successfully — without significant CAPEX in many instances.
Tapping the new technology in the management of the wastewater treatment ecosystem and the unmatched value and durability of new electro-ceramic exchange membranes can bring relief to industries feeling the heat and concerned about environmental impact.
Greg Newbloom, PhD, is the founder and CEO of Membrion, a cleantech startup focused on recycling wastewater from harsh industrial processes. His leadership and entrepreneurial efforts are recognized by a half-dozen regional and national awards, including a ‘35 under 35’ honor from the American Institute of Chemical Engineering. Dr. Newbloom has 50 patents in addition to co-authorship of a textbook and 300+ citations on nine publications.