Making Power From Sludge: A Sustainable Solution For Wastewater Treatment
By James Chalmers
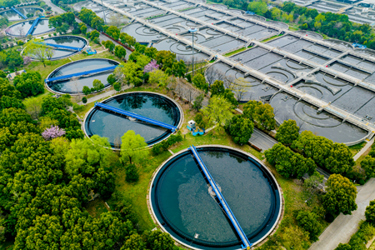
Sludge can go from a problem to a resource with energy recovery, but the process must be supported by the proper technology to truly be efficient and sustainable.
Worldwide, the volume of sludge — a byproduct of wastewater processing — has increased to over 100 million tons per year. This is driven in part by population growth and rapid urbanization, as well as broadening access to sewage systems. However, we currently only process half of the world’s wastewater, meaning that 4.2 billion people still lack access to safe sanitation. As these people gain access to this essential service, the volume of sludge will continue to increase.
Sludge has historically been considered a waste product. It was once commonly given away to farms for use as fertilizer or disposed of in landfills. However, increasingly strict legislation, such as the EU Landfill Directive1 and EPA Part 503 Biosolids Rule,2 have stopped this.
These restrictions are increasingly common around the globe. A recent project in Mumbai, India, required the plant to meet U.S. EPA standards, for example, while South Africa has its own strict rules.
Clearly, utilities must reduce the amount of sludge they produce. One promising option is anaerobic digestion, which is already common in developed countries and newer installations in emerging economies. Installing a new digester is expensive, but facilities can use the biogas it produces as a source of heat and electricity, reducing a plant’s operating costs and contributing to its sustainability.
Processing Sludge Efficiently
Sludge treatment involves several energy-intensive steps. It is screened and de-gritted to remove debris and then thickened and dewatered, traditionally using drying beds. More modern approaches used to speed up the process and treat greater quantities, such as in centrifuges or belt filter presses, are being adopted.
The sludge then undergoes thermal hydrolysis. This improves the biodegradability and viscosity of the sludge, as well as the biogas yield. It is now ready for digestion. To optimize this process, the sludge is heated to an optimal temperature for bacteria to carry out anaerobic digestion.
Anaerobic digestion reduces the amount of material and produces biogas, which consists mostly of methane and carbon dioxide mixed with other gases. The biogas is collected and purified, and then used in a combined heat and power (CHP) system within the treatment plant. Biogas can also be further refined into biomethane and sold as an additional source of revenue.
Biogas has already proven itself as a sustainable, cost-effective, and renewable energy source for generating electricity and heat, and as a fuel for transportation. As the price of electricity rises, there is an even bigger reason to invest in infrastructure to generate and capture biogas.
In many cases, electricity from biogas can produce upwards of 50% of a plant’s energy consumption. However, this requires the plant to complete every processing step as efficiently as possible.
The Role Of Advanced Motors, Drives, And PLCs
Processing sludge and using it for energy involves a range of motor-driven equipment, such as pumps, agitators, centrifuges, belt presses, and mixers. Ensuring that the correct equipment is specified is essential to maximizing efficiency and keeping costs down. Fortunately, modern motors, drives, and programmable logic controllers (PLCs) achieve the high level of efficiency and precise control needed for effective sludge treatment and energy conversion.
Electric motors are key to every step of wastewater processing. They must be designed to withstand the harsh, corrosive environment of wastewater treatment facilities. However, older motors are very inefficient. Upgrading to a newer, more efficient motor can significantly reduce the energy input required to process sludge into biogas, increasing the net energy output.
In applications that do not require constant full-speed operations, further efficiency can be achieved by pairing motors with variable speed drives (VSDs), also known as variable frequency drives (VFDs), or simply drives. A drive controls a motor’s speed and torque to match the requirements of the task. Any time the motor is not at full speed, it saves power. Because of the nonlinear relationship between speed and power consumption, slowing a motor by just 20% cuts its energy use by 50%. The most energy efficient class of motors, IE5, uses synchronous reluctance motors (SynRM) paired with a drive to minimize energy losses.
Drives also offer advantages in terms of precise control. Operators can use drives to adjust variables such as flow rate and mixing intensity to reduce energy consumption and extend the lifespan of equipment.
PLCs can be added to a system to automate it. PLCs can monitor variables such as temperature, pH, and dissolved oxygen levels and adjust processes accordingly. In digester applications, PLCs maintain the ideal conditions so the bacteria responsible for breaking down the organic matter can operate optimally.
The Top Priority: Safety
Drives and PLCs are also essential for safety. Modern drives include built-in functional safety features such as safe torque off (STO). This can reduce the number of injuries and accidents caused by equipment like belt presses. PLCs can also be used to detect and respond to equipment malfunctions, ensuring that processes run smoothly and safely.
In addition to the hazards of moving equipment in any application, biogas is highly flammable. Therefore, facilities must select matched motor-drive packages with ATEX-certified safety functions. ABB has designed ATEX motor-drive packages with SynRM motors that achieve the highest levels of safety, efficiency, and performance.
Giving Back To The Grid — Biogas In Action
The operators of a water treatment plant in Bocholt, Germany, aimed to reduce its environmental impact. They selected the latest SynRM motors for their sludge pumping station, which greatly reduced the amount of energy required.
They also used efficient motor-driven centrifuges to rapidly dewater the sludge before pumping it into two digesters. The biogas produced by these digesters — combined with the site’s biomass, wind turbines, and photovoltaic panels — generates approximately 6.3 million kilowatt hours of electricity per year. The plant only consumes around 3.3 million kilowatt hours, so it sells the surplus to the local grid.
Elsewhere in Germany, in Trier, utility company Stadtwerke Trier has used biogas to operate a carbon-neutral facility for more than five years. It uses gas from two cogeneration plants to generate approximately 2.7 million kWh of power annually. However, this sophisticated system faced issues with “network impurities” from electrical harmonics that arose during switching. Harmonics can cause damage to equipment, shorten its lifespan, and cause power outages, among other issues.
Fortunately, the Trier facility was able to identify the source of the issue — ultrasonic wave generators — and installed active filters. When the facility added a dewatering facility in 2021, to enable storage of dried sludge for use in the cold winter months, operators selected 12 ABB ultralow harmonic ACQ580 water and wastewater drives. These drives reduce harmonic content to a negligible level while improving energy efficiency.
Finding Sludge’s True Value
Given the immense potential of sludge, it is surprising that it was ever given away. With appropriate equipment and safety measures in place, sludge can be harnessed to produce sustainable heating and electricity, significantly cutting down on a plant’s operating expenses and environmental footprint.
References
- https://eur-lex.europa.eu/EN/legal-content/summary/landfill-of-waste.html
- https://www.epa.gov/biosolids/biosolids-laws-and-regulations
About The Author
James Chalmers is vice president, global water and wastewater sales for ABB Drive Products (https://new.abb.com/drives/segments/water-and-wastewater).