What Everyone Should Know About Enhanced Biological Phosphorus Removal
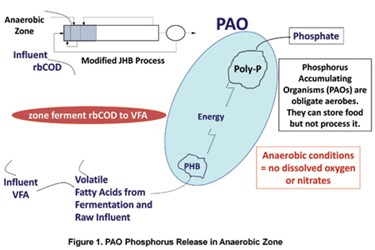
By Ed Kobylinski, Mark Steichen, Dave Koch, Dave Bunch, and Tom Ratzki
As phosphorus effluent restrictions continue to mount, many utilities will need to step up their treatment. Black & Veatch advises on the potential of EBPR.
Regulatory activity in the Midwestern United States, as in other parts of the country, has spurred increased interest in nutrient management among utilities throughout the region. Discharges into the Great Lakes or water quality-impaired streams as defined by each state will soon be required to meet nutrient discharge limits. This raises questions for utilities about how to cost-effectively and sustainably achieve compliance with new phosphorus discharge limits.
The Illinois Environmental Protection Agency (EPA) is considering a total phosphorus (TP) effluent limit — probably 1 mg/L TP — as the first step, and other state agencies are likely on a similar tack. Utilities that need to meet these lower limits will want to consider enhanced biological phosphorus removal (EBPR). Unfortunately, the biological removal of phosphorus is frequently misunderstood; a solid understanding of the EBPR process and the needed wastewater characteristics that drive EBPR is essential for effective use of the technology.
Enter EBPR
The U.S. EPA’s first major technical publication on phosphorus removal, which dates back to April 1976, addressed chemical precipitation of phosphorus. The discovery of biological phosphorus removal has since revolutionized the wastewater treatment industry with a lower operating cost and ability to produce a valuable end product with a high agronomic value. But understanding influent data analysis requirements, the role of fermentation, and how collection system practices affect the process is necessary for effective planning.
EBPR is simply the biological uptake of phosphorus by selected microorganisms called phosphorus-accumulating organisms (PAOs). While the actual uptake of phosphorus occurs under aerobic conditions, PAOs must first be conditioned by exposure to volatile fatty acids (VFA) under anaerobic conditions. PAOs store food under anaerobic conditions and then process the stored food once under aerobic conditions. The preferred foods for PAOs are volatile fatty acids (VFA): acetic, propionic, and butyric acids.
PAOs expend energy to transform VFAs into a chemical form for storage, and they obtain energy for VFA storage by breaking phosphorus bonds within themselves. This results in the release of ortho-phosphate which is the conditioning step needed to trigger the aerobic “luxury phosphorus uptake.” If PAOs are exposed to enough VFA, they will deplete their energy reserves and become stressed. This stress causes PAOs to overreact and accumulate more phosphorus in their chemical energy storage banks.
While good aeration is all that is needed for phosphorus uptake to occur, the aerobic uptake of phosphorus is dictated by the amount of VFA stored and energy/phosphorus released in the anaerobic zone. Therefore, EBPR process success is primarily determined by influent wastewater quality and the amount of VFA that is present in proportion to the amount of phosphorus to be removed.
Fermentation Can Help Fuel The Process
The recommended minimum ratio of chemical oxygen demand to phosphorous (COD:P) is 40:1. This influent COD:P ratio is correct but misleading. The authors have seen plants with a >40:1 COD:P ratio work great for phosphorus removal, while other plants with a similar ratio struggle. EBPR performance varies from plant to plant with similar influent wastewater COD:P ratios because not all COD is the same when it comes to EBPR.
Some wastewater treatment plants (WWTPs) have enough VFA in the influent to satisfy the EBPR needs for good phosphorus removal. If the VFA as COD:P ratio is over 8, EBPR will perform well. Good EBPR performance is defined as producing an effluent ortho-P concentration below 0.3 mg/L. Because effluent permits focus on TP, a 1 mg/L TP effluent permit can be easily met with a 0.3 mg/L ortho-P concentration and an effluent TSS less than 10 mg/L. Although having a sufficient supply of VFA in a WWTP influent is ideal, some plants have little VFA in their influent and still achieve effective EBPR performance without chemical addition.
How can an EBPR system consistently remove phosphorus to a very low concentration with a low or variable supply of influent VFA? The anaerobic zone needed for EBPR performs multiple functions. The primary function is the uptake of VFA by PAOs, but PAOs constitute only a small subset of the bacterial population in the mixed liquor suspended solids (MLSS) in the anaerobic zone. The rest of the bacteria are switching gears to ferment organic compounds to obtain food and energy (Figure 1). These facultative bacteria do not consume VFA; they break down complex soluble organic chemicals to form VFA, allowing the PAOs to take up VFA and release phosphorus. Therefore, the anaerobic zone in an EBPR plant simultaneously conditions PAOs and provides an environment for additional fermentation of soluble organics to VFA.
The analytical tool used to predict the amount of VFA that can be formed is the soluble readily biodegradable COD fraction or rbCOD. The rbCOD concentration is derived from a special flocculation and filtration treatment procedure — called filtered flocculated COD (ffCOD) — to pretreat the sample prior to COD analysis. Subtracting the effluent ffCOD (nonbiodegradable COD) from the influent ffCOD (total soluble COD) results in the rbCOD concentration. The ratio of rbCOD to P is a better indication of the performance of the EBPR process than the total COD:P ratio referenced in textbooks because only the soluble rbCOD will be fermented into VFA in the anaerobic zone. There is not enough time for suspended COD to be fermented to VFA in the anaerobic zone.
Figure 2 illustrates the variable relationship of rbCOD to P. As the fraction of influent rbCOD that is VFA decreases, the necessary rbCOD:P ratio for successful EBPR increases. If fermentation occurs in the collection system due to anaerobic activity in the collection system (odor issues at the WWTP headworks is good indication of this), the anaerobic zone does not have to provide much additional fermentation for EBPR to work well. Conversely, if fermentation does not occur in the collection system, it has to occur in the anaerobic zone for EBPR to work well.
The discussion thus far has focused mainly on the phosphorus release portion of the EBPR process because phosphorus uptake is covered through good aeration design. Keeping >2 mg/L DO residual at the head end of the plug flow aeration basin is the goal. The phosphorus release depletes the PAO of energy, which stresses the microbe. This stress causes the PAO to take up excess phosphorus in the oxic zone; if DO is limited at the front end of the oxic zone, the PAOs fail to uptake as much excess phosphorus.
Fermentation at a WWTP can take many forms. A dedicated primary sludge fermenter is common for plants that have primary clarifiers. Primary clarifiers can also be “activated” to enhance fermentation. In two-stage anaerobic digestion the acid digestion phase is essentially fermentation and can be used as a VFA source.
MLSS fermentation is another viable option for carbon augmentation and PAO conditioning. If the influent is short on rbCOD, a simple strategy of cycling mixers on and off in the anaerobic zone allows MLSS to settle and increase the solids retention time in that zone, which results in formation of additional rbCOD/VFA. If more soluble material is needed, a separate return activated sludge (RAS) or MLSS fermenter will provide more efficient fermentation. Compared with RAS fermentation, MLSS fermentation ferments a higher fraction of primary effluent volatile solids and colloidal material absorbed by the mixed liquor, which increases carbon available for fermentation.
Fermentation in the collection system is desirable for operation of an EBPR system, but can present problems for collection system staff due to undesirable side effects such as odor complaints and sulfide-induced corrosion. Chemical addition and physical modifications to the collection system can be implemented to reduce sulfide production, although such changes also reduce fermentation to make rbCOD.
Odor and sulfide-corrosion control methods include addition of oxidants (e.g., chlorine, hydrogen peroxide) to destroy hydrogen sulfide or injection of oxygen or addition of nitrate to modify the sewer environment from anaerobic to anoxic or oxic and stop formation of hydrogen sulfide (Kobylinski, et al. 2008). Such chemical additions are intended to stop fermentation and reduce sulfide concentration in the sewer, but they also result in the loss of rbCOD, thereby hurting EBPR performance. The only proven sulfide control approach that will not significantly impact EBPR performance is the addition of iron. Iron specifically reacts with hydrogen sulfide but does not impact rbCOD concentrations and has no impact on microbial activity to produce VFA.
Where To Start
If you’re now wondering whether you have to choose between fermentation in the collection system (risking infrastructure damage and odor complaints) or chemical addition to remove phosphorus, it’s time to step back. Utilities that are considering implementation of EBPR to meet new or lower phosphorus limits should begin with a comprehensive/coordinated plan for the collection system and WWTP improvements.
Comprehensive influent wastewater characterization can help you determine the quantity and reliability/consistency of the influent carbon source (rbCOD) to support EBPR. Knowing the incoming wastewater quality will help determine if the level of hydrogen sulfide control needed to protect a collection system from excessive corrosion will interfere with or stop collection system fermentation, making it necessary to add a fermentation process for reliable EBPR at the WWTP site.
To make sure utility investments culminate in facilities that meet future capacity needs and comply with anticipated permit requirements, WWTP designers tend to make relatively conservative assumptions. Such assumptions help address unknowns such as how much VFA or rbCOD is available in the influent throughout seasonal fluctuations but tend to increase project costs. Availability of historical data reduces the need for assumptions, which in turn reduces capital costs.
Additionally, arbitrarily reducing VFA in collection systems to control odors may be counterproductive. The best approach in planning is to understand the balance between odor generation in the collection system and the cost of VFA production at the WWTP. Ultimately, sampling today to generate a good historical database of these different influent wastewater characteristics will reduce the need for assumptions and allow better definition of the facilities necessary for plant upgrades to meet new phosphorus effluent limits. Good influent characterization builds confidence that the new facilities will achieve permit compliance. It also allows for optimized design and operations to reduce capital investment. Good sampling data provides a reasonable basis to defend the plant upgrade design to regulatory review, especially when phosphorus removal is new to a state.
We all know the value of starting with the end in mind. If phosphorus removal is your goal, enhanced biological phosphorus removal may be your best direction. Careful consideration of process needs and related side effects combined with maximum knowledge about your influent characteristics and system needs can smooth potential bumps on the road to compliance. Planning and influent sampling today can save you money in the future.
Reference
Kobylinski, E., Van Durme, G., Barnard, J., Massart, N., Koh, SK; How to overcome hydrogen sulfide problems while preserving biological phosphorus removal, WE&T Operations Forum, October 2008
Ed Kobylinski is a Senior Treatment Process Engineer and Mark Steichen is Director of Wastewater Process in the Kansas City, MO, office of Black & Veatch. Dave Koch leads Black & Veatch’s Chicago office. Dave Bunch has been an Engineer/Project Manager for numerous EBPR projects in the Midwest and Tom Ratzki is the Midwest Client Relations Director in the St. Louis, MO, office of Black & Veatch. All have considerable experience with nutrient management.