The Future Of Fracking: Evaluating Emerging Technologies
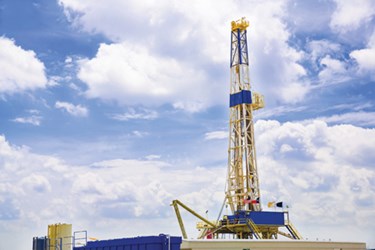
How can the U.S. and other countries profit from hydraulic fracturing AND protect water resources? New technologies hold the key to environmentally responsible shale-gas production.
By Frank A. McGrew, IV, managing director and Jay Gorman, VP, Raymond James & Associates, General Industrials Group
With conventional oil and gas production peaking and entering a period of long-term decline, producers are increasingly looking to new resources such as shale gas, oil sands, heavy oil, etc. to meet growing global energy demand. These unconventional oil supplies require nontraditional, water-intensive production technologies like hydraulic fracturing, or fracking, for extraction. Fracking requires 2 to 5 million gallons of water to drill one well1 with a large amount returning to the surface as produced water. Exploration and production (E&P) companies are facing significant water management challenges as water sources are becoming more limited, options for disposal are declining, and the threat of more stringent regulation is increasing. With unconventional production expected to continue to grow significantly as a percentage of the world’s liquid fuel supply, the oil and gas water management market is projected to expand at a compound annual growth rate of 6.0 percent from 2014 to 20202. The highest growth is anticipated in produced water treatment services and equipment as innovative approaches to reuse become cost effective solutions to industry demands.
Global Oil And Gas Water Management Market
Unconventional drilling in the U.S. alone generates an estimated 280 billion gallons of produced water annually3, making wastewater management and disposal a major component of the fracking process. The most common manner of disposal is reinjection underground into a closed reservoir. This practice typically involves trucking the wastewater long distances to disposal wells, which can result in 500 to 1,500 truckloads of water per fracking job. To date, this trucking and injection method has been the most cost-effective means of disposing frack and produced water, and, as such, it currently accounts for over 80 percent of dollars spent on oil and gas water management. However, trucking and disposal are fraught with numerous side effects, which likely will accelerate the development of alternatives. The most obvious side effect of utilizing injection wells to dispose of contaminated water is the requirement that new fresh water be utilized for each fracking job. With numerous oil and gas basins facing significant shortages of water, the failure to recycle frack and produced water puts further stress on this limited resource. In addition, the thousands of truckloads required to service each well have resulted in billions of dollars in damage to roads. Some areas, such as the Marcellus Shale, feature extremely limited injection well availability, necessitating that water be trucked hundreds of miles to the nearest disposal site. Even though several states have started to collect fees from E&P companies for infrastructure maintenance, they typically have not been sufficient to cover repairs, leaving taxpayers to make up the gap. Furthermore, frack hauling traffic has produced concerns over unsafe conditions for local drivers, as the areas of many well sites require the use of narrow country roads, and truck drivers may be fatigued after working long hours.
The alternative to trucking water to injection wells is to treat the produced water on-site, removing salts, chemicals, and other compounds in order to make it fit for reuse. With increasing attention to water consumption and protection of sources, state governments are starting to promote and mandate recycling of produced water. Texas has eased permitting requirements and is potentially moving toward deregulation altogether, making it easier to recycle. Legislation is also pending which would only allow disposal of produced water if it cannot be treated and add recycling to the water protection segment of the state’s Natural Resources Code. In Pennsylvania, the Center for Sustainable Shale Development, a partnership of prominent energy companies, environmental organizations, and philanthropic foundations formed in 2013, claims that its members will follow voluntary standards that are more rigorous than state laws, including 90 percent recycle rates of produced water.
Recycling wastewater from fracking has traditionally utilized treatment methods such as reverse osmosis, electrocoagulation, distillation, ultraviolet (UV) disinfection, dissolved gas flotation, ozonation, ion exchange, and evaporation. While there is seemingly a solution to treat and reuse just about any form of contaminated water, the challenge is developing solutions that are cost-competitive when compared to trucking and disposal. A key limiting factor in traditional purification processes is the amount of energy required. However, many new technologies are emerging which offer the potential for cost-effective treatment by utilizing technologies that require far less energy, or utilize waste energy, to reduce costs and treat contaminated water more efficiently. See below for a number of companies that are utilizing innovative technologies to solve this ever-increasing problem.
Altela, Inc. offers a pressure-less mobile or stationary thermal distillation water treatment system which mimics nature’s hydrologic cycle of making pure rain water from seawater. Through the company’s proprietary technology named AltelaRain, produced water is placed into plastic containers, or small towers, where it is heated to create vapor. The vapor floats up until it hits cool air at the top of the tower. It then condenses into fresh water that trickles down to tanks below, leaving a small amount of leftover sludge for disposal. By removing the need for pressure (used in most other desalination processes like reverse osmosis), Altela’s technology does not require expensive pumps, valves, or costly amounts of electricity or man-made chemicals. Additionally, the heat used to start the treatment process is recaptured for further use as vapor condenses, releasing trapped heat, which contributes even more toward reducing energy costs.
Armada Water Assets, Inc. has designed a modular “treatment train” system combining a number of traditional treatment technologies and conventional components such as oil/water separators, aeration, electrocoagulation/precipitation, reverse osmosis units, and ceramic and carbon filter systems with a proprietary high shear reactor, which acts as a molecular accelerator. This high shear reactor dynamically accelerates the natural vibration and spin of molecules in the process stream. This decreases the energetic barriers to the separation of solvents from wastewater, reducing energy consumption and operating expenses involved with the treatment of produced water. Armada’s treatment trains can be used as mobile, temporary, or permanent solutions, and can be economically scaled and configured to meet specific local needs.
Ecologix Environmental Systems provides a mobile Integrated Treatment System (ITS) utilizing Dissolved Air Flotation (DAF), a long-proven method for separating solids from waste streams. In the DAF process, targeted chemicals are used to precipitate oils and solids out of suspension, and then a physical mechanism removes those solids from the water. The ITS consists of three primary components: one to control chemical application, another to mix the chemicals into the water, and a third to physically separate the solids from the water. The ITS solution is flexible to the specific needs of the formation and driller preferences, and the company claims it creates reusable water at or below the cost of sourcing, trucking, and well disposal.
Hydrozonix has developed a mobile, single-point, scalable, and modular treatment solution employing ozonation, hydrodynamic cavitation, acoustic cavitation, and electro-chemistry technologies. In this process, water enters the unit through two pipes traveling through static mixers that homogenize the water and initiate hydrodynamic cavitation. Extremely high temperatures and pressures from bubble collapse cause thermochemical decomposition and produce highly reactive hydroxyl radicals. Next, after passing through a mesh screen, ozone, a highly reactive oxidant that kills bacteria, is injected into the fluid. The highly ozonated water then enters flash reactors that accelerate ozone blending just before the water enters the reactor radially at multiple points. In the reactor, ultrasonic transducers create cavitation, again generating thermochemical decomposition and hydroxyl radicals. The passage of electricity through the water is the primary driver in precipitating hardness salts from the fluid. Ultrasound breaks apart the precipitated salts into nano-sized suspended particles that will not cause scale. The electrical field also reacts with oxygen in the water to create more hydroxyl radicals which assist in further oxidation of bacteria. Finally, the water leaves the reactor traveling through another large section of static mixers and electrodes to further augment treatment. The water, free of bacteria and scaling tendencies, is pumped out of the system, ready for use.
Oasys Water, Inc. offers forward osmosis technology for high recovery desalination of wastewater with salt concentrations up to five times higher than seawater. This process uses a proprietary draw solution made up of thermolytic salts to naturally draw water across a patented semipermeable membrane, leaving unwanted salts and contaminants behind. Low temperature heat then transforms the remaining mixture of solution and fresh water from liquid to vapor, leaving behind clean, potable water. The process can utilize steam or heat from a variety of sources and requires no feed water boiling or high pressure pumping, providing a more sustainable treatment approach at lower cost.
OriginOil has designed a high-speed, chemical-free treatment technology called Electro Water Separation (EWS). This consists of a two-step process starting with electrocoagulation where mild electrical impulses are applied in long tubes, causing organic contaminants to clump together. Then, during electroflotation, this clumped material enters a second stage where low power electrical pulses generate a cloud of micro-bubbles that gently lift the concentrated pollution to the surface for removal, leaving clean water behind. At the heart of the EWS technology is a proprietary process control unit (PCU) that controls the entire process and customizes the power requirements of each application. The PCU’s auto-adaptive features reduce operator intervention and standardize operating parameters while communicating with OriginOil cloud servers, facilitating authentication, remote operation, diagnostics, and updates to maintain maximum operating uptime in the field. OriginOil combines its EWS technology with other treatment processes that may include ultrafiltration, reverse osmosis, and ion exchange in its CLEAN-FRAC 1000 customized, end-to-end-produced water treatment solution.
While it remains to be seen which, if any, of these new technologies will achieve widespread adoption, they do offer the promise of an improved fracking process with meaningful reductions to costs and the water use of oil and gas production. The challenges surrounding water management in the oil and gas industry are vitally important to solve, as they are critical to the country’s economic and environmental future. Perhaps what is certain is that the significance of these challenges will ensure that change and innovation will continue to characterize this industry and show that substantial opportunities exist for solutions that prove most effective.
About The Authors
Frank A. McGrew, IV, managing director, Raymond James & Associates, General Industrials Group, has represented numerous public and private firms in both advisory and principal roles on such issues as strategic management, corporate growth, financing, restructuring, and overall capitalization. During his nearly 25- year career, he has raised more than $4 billion in capital and advised on nearly $10 billion of strategic transactions for numerous entities throughout the world.
Jay Gorman, VP, Raymond James & Associates, General Industrials Group, has more than 10 years of corporate finance experience, having worked on a myriad of successful acquisitions, divestitures, joint ventures, partnerships, and other strategic initiatives for diversified industrial and basic manufacturing companies.
Raymond James & Associates actively covers the water/wastewater sector through its General Industrials investment banking group and has advised numerous clients in the industry.
References
1. U.S. EPA
2. Global Water Intelligence
3. Environment America