Tangential Flow Separation: A New Way To Treat Waste
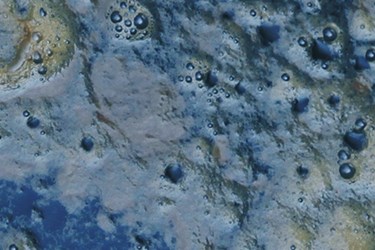
By J.H. Wakefield
Can “leaky hoses” really be considered an innovation? The answer is yes — when applied (ingeniously) for liquid/solids separation.
Most water treatment professionals are familiar with the categorization of waste treatment processes into three general segments: 1.) sedimentation/ settling of particulates in the waste stream and concomitant separation of these from the liquid phase of the waste stream as a first category; 2.) biological treatment technologies of one sort or another on the separated liquid phase as a second category; and 3.) tertiary treatment (usually chemical or physical in nature) to ensure removal of specific waste products that must be removed before any resulting effluent is discharged into the environment.
There are a plethora of different devices and processes that arise to address these various segments of the waste treatment process. In the following explanation, we shall examine a new technology that is applicable to both the initial segment (solid particulate removal) as well as to the final “polishing” process of the waste stream.
Understanding Particulate Removal
Before we get started, it might be a good idea to review the basics of particulate removal in the entire wastewater treatment process. Particulates are assigned to categories depending on their physical state and sometimes even their chemical properties. The categories are: settleable solids, suspended solids, colloidal particulates (“solutions”), and soluble solids (i.e., solvated solids with the standard solvent being water, although other solvents are occasionally encountered).
Settleable solids depend on size and density as separation characteristics, but the process is also dependent upon temperature and particularly the velocity of the waste stream. Turbulence is also a variable, though it, too, is generally treated as a velocity-related parameter. Suspended solids are those of smaller size that do not readily settle out, so one normally utilizes coagulants/flocculants to effect the process. Coagulants develop a sticky, gummy mass that usually consists of a gel-like hydroxide (aluminum, iron, or even calcium) to entrap these smaller particulates as they become enmeshed in the formed matrix. A further step is completed as these trapped and bound particulates are sequestered in the matrix formed, and flocculants increase the extent of the matrix.
Colloidal particulates are those that are so small they do not spontaneously separate, and they carry an adsorbed electrostatic charge surrounding the particulate. This charged “coating” is referred to as the Stern Layer and has a thickness of a single hydrated ionic layer tightly attached by electrostatic forces to the colloidal particulate forming a first inner layer of charges. Because the colloidal particulate is electrically charged, it attracts ions and other colloidal particulates of the opposite sign. The particle and the attached ions of opposite sign form an electrostatic double layer. Additional ions of opposite sign to that of the colloidal particulates also accumulate next to the Stern Layer. These form a diffuse layer. These colloids are agglomerated by essentially tampering with these electrostatic charges in one way or another. Depending on the nature of a particular colloidal particulate, they may be “salted out,” bridged by means of various polymers, removed by ion-exchange mechanisms, and/or flocculated by any and all of the above.
The last category of particulates to be removed is solvated particulates (usually molecular in nature, but not always) that are chemically treated — that is, reacted with some other functional group that results in their being bound or sequestered in the gel matrix. It is here that ion-exchange becomes a predominant “player.”
Keep in mind that no matter what the nature of these individual particulates is, they are “converted” from being a member of the liquid phase to being a member of the solid phase. The final problem that arises is separating these two phases as efficiently and completely as possible.
New Separation Technology
It has come to my attention from several client companies that there is a new technology that works both in the initial and tertiary treatment of these waste streams. Several patents have been issued in this regard, and I have considered it best to address them as tangential flow separators. These devices are liquids/solids separators employing a unique principle, whereby “leaky” hoses utilize a laminar flow vector for the solid phase and a tangential flow vector for the liquid phase. The fluid path is contained within a tube (or hose, if you like), and the solid phase is forced down and out of the lumen of the tube. The liquid phase is collected by a mesh membrane of sorts and, for you chemical engineers out there, is related to a modified Frasch process minus the high pressures and temperatures. The solid phase continues down the tube where it is collected. The result is the removal of the solid phase from the liquid and the dewatering (or desolvating, depending on the solvent) of the solid phase.
As it results in removal of particulates and their concentration for disposal or other applications, these may be considered as primary treatment devices. If the waste stream has a specific character, such as a waste stream from a plating operation, these devices could be used as such.
But that’s not the whole story, nor the designed intent. Tangential flow separators have, in fact, been designed as tertiary treatment devices to address recalcitrant waste streams with difficult-to-remove regulated and/or dangerous components. This is the result of a “package” of coagulants/flocculents designed specifically to address these situations. A not uncommon method of addressing these problems involves the oxidation of offending ionic species (such as Cu++, Cd++, Pb++, and others), as well as sequestering those anions (PO4 ≡) that form insoluble precipitates and/or complex ions, and then utilizing the principle of ion-exchange to remove other offending anions (NO3-). This involves a clay (usually a montmorillonite), an inorganic coagulant (alum or ferric ion compound), and a specially formulated polymer (usually a cationic polymer) to complete the removal process.
The big advantage of this tangential flow separator technology is that it lowers the cost by controlling the cost of the polymers necessary (though not eliminating their usage) and by allowing the use of zeolites (specifically, clinoptilolites) to both remove and bind a variety of offending ionic species. Clinoptilolites are zeolites that function as scavengers for both anions and cations become highly charged and are readily removed as larger particulates from the liquid phase.
Considerations Regarding Flocculants
It is incumbent upon one wishing to separate solid and liquid phases to have them clearly delineated. The more completely they are delineated, the more effective the results.
To this end, different coagulants/flocculants are employed depending on the waste stream that is encountered. Included among these are natural flocculants such as the montmorillonite clays (Bentonite, for example), as well as various volcanic clays including the various forms of zeolites (clinoptilolite, for example). Either mixtures of these coagulants/flocculants are used, or possibly those with additions of processing chemicals including various inorganic salts and polymer ion-exchange moieties, in order to effect an acceptable separation for particular waste streams.
In any waste stream, there are both suspended and dissolved solids. The separation technology, whatever it is, is efficacious only insofar as it is capable of aggregating or precipitating these differing physical forms. So, both a physical and chemical reaction are usually necessary. Dissolved solids are precipitated, suspended solids are unsuspended, and both of these components are then collectively aggregated and removed via the tangential flow separation technology. How this separation occurs in any system is essential to understanding the functioning of the system and the rationale for its design.
How And Why It Works
Dissolved solids are the first to be considered. There are two ways to remove them: First, solubility may be altered by chemical means. To this end, the addition of various salts may affect their solubility and result in the formation of an insoluble precipitate. Secondly, these dissolved solids may be sequestered as solids in various complexes, which themselves are insoluble. By these means, virtually any dissolved solid can be removed. All one has to do is find an agent that will precipitate or sequester it. Bentonite is an economical and effective choice as a carrier, especially if it is treated to effect a particular separation.
The suspended solids are next on the agenda for particular waste streams. These are a bit more complex as they vary widely in chemical structure and even in the mechanism of their suspension. Some are suspended as a result of their size (either very large or very small). Those that are very large depend, for the most part, on the velocity of the waste stream and its temperature. Smaller ones usually depend on surface charge.
In removal, large ones are mostly an annoyance, but small ones can be a real problem, as surface phenomena are involved. The key to removing these particulates is to find what charge they carry, and, if possible, what engendered the charge. This is addressed by providing an opposite charge to aggregate the particulates (opposite charges attract). How this is accomplished may require a coagulant/flocculant that is itself oppositely charged. Most of the microparticulates carry a negative charge; therefore, coagulants/flocculants should usually have a positive surface charge. Many of the Bentonites do have a positive surface charge (remember they are ion-exchangers); if a more or differently charged surface is required, the addition of an aluminum salt can alter the structure of the Bentonite or can even be sequestered in other additions to the mixture, such as the various zeolites (which are also ion-exchangers [water softeners]). The bases resulting from aluminum and ferric/ferrous iron (aluminum and iron hydroxides) are commonly used as coagulants/ flocculants in water treatment and wastewater plants presently.
The tangential flow separator system is designed to add the necessary amount of coagulants/flocculants in order to aggregate the waste stream to an acceptable degree. This is affected by an air-driven mixer that injects the flocculant stream concurrently by mixing it into the waste stream. This mixer can be adapted to deliver any surface charge necessary to effect coagulation/ flocculation. Exactly how and at what step prior to filtration depends on the nature of the waste stream, as well as the physical parameters such as velocity, temperature, and particulate charge on the suspended particulates within the waste stream.
The tangential flow separator is then “charged” as the flocculant-treated waste stream enters the lumen of the separatory part. At this point, the solids are moved “down the line,” and the fluid fraction is separated and directed tangentially to the flow. This action results in a filtration situation in which the liquid fraction is flowing more or less perpendicular to the linearly directed flow of the solids as they proceed down the lumen. This results in the tangential flow separator acting as a “leaky pipe” for the fluid phase removal and as a solids concentrator for the solids moving down the separator’s lumen.
Evidence regarding the separation efficacy resides in the before-and-after values of various impurities “of interest” in a particular waste stream that are determined from the seperated liquid phase. Of course, the solid phase likewise shows the efficacy of the process by the amount of fluid retained in the cake and by the amount of coagulant/flocculant comprising the solid phase of the treated solids emanating from the lumen. As flocculant inclusion into this cake is quite important from a regulatory viewpoint (yet limited as a processing aid), the amount present in the final cake determines the efficacy of the process as a whole.
About The Author
Dr. J.H. Wakefield is a consulting scientist/engineer with more than 30 years of experience in water/wastewater treatment. He holds advanced degrees in microbiology and physical/analytical chemistry and has been a practicing chemical and environmental engineer for many years.