Opportunities And Tips For Expanding Water Resource Recovery Facilities
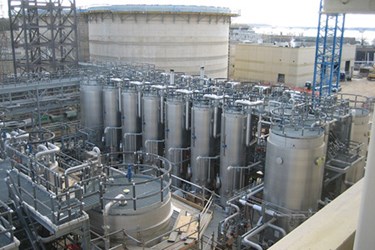
Transform your residuals and biosolids from a burden to a benefit — for both your utility and the environment.
By Todd Williams, expert in residuals and biosolids management, CH2M HILL
Managing residuals and biosolids can account for nearly half the treatment costs at a water resource recovery facility; however, residuals and biosolids contain significant amounts of nutrients and energy that can provide value to utilities — both through beneficial reuse and revenue if reclaimed and sold. In July 2013, the Water Environment Federation (WEF) and the National Biosolids Partnership released a study that looked at water resource recovery facilities (WRRF) in the U.S. and the emerging opportunities for residuals and biosolids. More than 5,100 facilities participated in the survey. The majority of the facilities that participated in the survey treat more than 1 MGD, and about 50 percent of them currently use anaerobic digestion to process solids.
Resource Recovery Potential
The study produced some interesting findings, which I like to characterize as “3-3-6” — three times as many WRRFs do not have anaerobic digestion as those that do; three times as many WRRFs with anaerobic digestion don’t generate power or operate plant equipment with recovered energy as those that do; and six times as many WRRFs don’t import fats, oil, and grease (FOG) or high-strength waste-to-feed digesters as those that do. Given these results, there is significant opportunity for development of energy recovery at WRRFs in the next decade.
The Resource Recovery Model is not complicated. Rather than just accepting and treating wastewater to recover energy, WRRFs with anaerobic digestion can accept additional materials beyond wastewater, including:
- High-strength liquid wastes (HSW)
- Fats, oils, and grease (FOG).
Using these materials and anaerobic digesters, the facility can produce multiple products beyond reclaimed or recycled water, such as:
- Nutrients
- Biosolids (which provide carbon and nutrients for agriculture/farm land)
- Renewable energy (power and heat).
In addition to creating these products, adding FOG and HSW directly to digestion offers the following benefits:
- Improves sewer and WRRF performance
- Provides revenue stream from tip fees
- Generates significant amounts of biogas at low hydraulic loading in anaerobic digestion
- Creates significant cost savings from producing biogas when coupled with cogeneration
- Reduces greenhouse gas footprint and energy dependence.
Given that incorporating FOG and HSW resources is a relatively new process, there is little in the way of standard operating procedures for utilities looking to add these materials to a WRRF. However, the practice is growing rapidly, and utilities that are considering incorporating FOG and HSW can benefit from the lessons learned at existing WRRFs. Key considerations for utilities considering this alternative include the reliability, consistency, and availability of each material as a feedstock, as well as its collection network to move the FOG or HSW to a receiving station at the WRRF. Additionally, there are special requirements for receiving, holding, and transferring FOG and HSW on a continuous basis, so the utility must consider these when evaluating the benefits.
Leading By Example: Real-World WRRFs
Recognizing the benefits of resource recovery, numerous facilities in the U.S. have implemented anaerobic digestion to create biogas and are achieving significant value and savings to their bottom line. Gwinnett County, GA, and Johnson County, KS, for example, have each reduced its plant’s electric usage by about 50 percent through the development of facilities that receive and process FOG and HSW in their existing anaerobic digesters.
California’s East Bay Municipal Utility District (MUD) is a prime example of how one utility has incorporated resource recovery into its business model. The utility’s original facility, which included three engines installed in 1985, was designed to meet 40 to 50 percent of East Bay MUD’s demand; however, the utility experienced frequent flaring of excess biogas. In 2011, the utility expanded its operations, adding an advanced 4.6-megawatt biogas turbine to increase its capacity from 6.5 to 11 megawatts. On average, the expansion enables the utility to produce enough biogas to generate 6 megawatts of electricity, meeting 100 to 120 percent of demand. The plant requires only about 5 megawatts to operate, so by selling its surplus energy (renewable energy) to the grid at a premium price, in 2013, East Bay MUD became the first wastewater treatment plant in the U.S. that is also a net electricity provider. Adding the turbine has enabled East Bay MUD to reduce air and greenhouse gas emissions, helping achieve its sustainability goals, while increasing its operational reliability.
Another good example of how one utility is putting resource recovery to work to improve its bottom line is the District of Columbia Water and Sewer Authority’s biosolids management program. DC Water, one of the largest water and sewer utilities on the East Coast, is leading the industry and truly reinventing biosolids technology at its 391 MGD Blue Plains Advanced Wastewater Treatment Plant in Washington, D.C. Developing the first Cambi thermal hydrolysis/digestion/ combined heat and power system in the U.S., Blue Plains will reduce biosolids quantities by 50 percent; cut greenhouse gas emissions by approximately 40 percent; generate 14 megawatts of clean, renewable power; and greatly improve product quality (Class A) that can be used for land application. When the facility finishes start-up and reaches full capacity later this year, it will save an estimated $20 million annually through its biosolids program alone.
Green Bay, Wisconsin’s Green Bay Metropolitan Sewerage District (GBMSD) is also implementing biosolids and resource recovery processes to effectively generate and utilize recovered energy. When faced with stricter environmental compliance standards and solids processing capacity issues, GBMSD enlisted the help of CH2M HILL to develop a Solids Management Facility Plan, known as the Resource Recovery and Electrical Energy Generation System or R2E2 Project. The plan includes building two anaerobic digesters and an incineration facility that, in combination, will break down biodegradable materials into a beneficial material and reduce the plant’s overall electrical energy usage by nearly 75 percent. The R2E2 Project will help GBMSD meet its sustainability and efficiency goals. The project is expected to be completed in the next several years.
Looking at case studies from across the U.S., I close with several tips for utilities interested in leveraging resource recovery to meet energy reduction goals:
- Include resource recovery evaluations as part of solids management planning efforts.
- Consider resource recovery improvements as part of any plant upgrade project. Synergies can usually be identified with other expansion efforts to minimize costs over independent projects.
- Whole plant modeling can and should be used to evaluate energy use and greenhouse-gas impacts of various alternatives to minimize energy use and maximize energy recovery.
- Consider public/private partnerships (PPPs) to lower capital outlay and minimize risk.
About The Author
Todd Williams, todd.williams@ch2m.com, is an expert in residuals and biosolids management. A frequent presenter, he is also a contributing writer to many books and articles about biosolids and residuals management, composting, and odor control, including the recently published WEF/WERF/EPA Solids Process Design and Management Manual. He graduated from Virginia Tech and is the past chairman of the WEF’s Residuals and Biosolids Committee. Todd works out of CH2M HILL’s Richmond, VA, office.