Freeport Wastewater Treatment Plant Saves Money And Energy With Hybrid Blowers
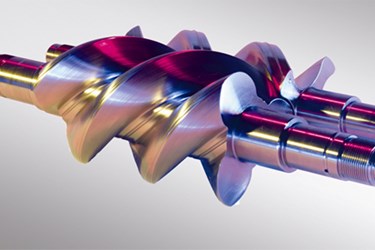
By Beth Brindle, Water Online
Best known as the home of outdoor retailer L.L. Bean, the community of Freeport is a popular summer destination on the shore of Casco Bay in southern coastal Maine. In 2010, the Freeport Sewer District brought in engineering firm Woodard & Curran (also of Freeport), to conduct an energy analysis of the Freeport Wastewater Treatment Facility. The assessment revealed that the Freeport plant consumed more than 8.9 kBtu per gallon of wastewater treated, more than double the national average of 4.1 kBtu per gallon. While an outdated oil heating system contributed to the overall inefficiency, the plant’s 30-year-old multistage centrifugal aeration blowers accounted for as much as 80 percent of the electricity consumption.
Get unlimited access to:
Enter your credentials below to log in. Not yet a member of Water Online? Subscribe today.