Debunking The Top 5 Myths Of Tank Repair

By Kevin Westerling,
@KevinOnWater
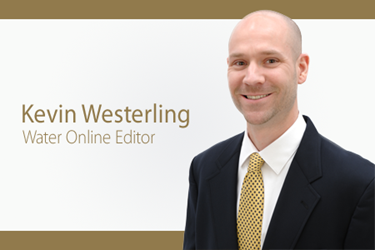
Direct from a tank repair expert, remain ignorant to these common pitfalls and misperceptions at your own peril.
As tanks age, they will inevitably need upgrades and repairs. When the time comes, owners can rely on industry standards, regulatory guidelines, and the advice of engineers and tank consultants to ascertain their needs and set a plan of action. Unfortunately, there is a fair amount of misunderstanding and misinformation surrounding tank repair, often resulting in inadequate or even unnecessary work.
I learned this surprising fact during a session presented by Christine Gunsaullus of Mumford-Bjorkman Associates (MBA) at the recent Pennsylvania Municipal Authorities Association (PMAA) conference. Gunsaullus shared the following five myths about tank repair in an effort to help owners keep costs down as they improve the condition and lifespan of their tanks.
Myth #1: Pressure Grouting Under The Bottom Is A Best Practice
According to Gunsaullus, some tank inspectors/contractors will recommend pressure grouting under the tank, a process to firm up the foundation, with virtually every job. However, this $20,000 to $30,000 process is rarely needed, as the weight of a filled tank settles the tank bottom down so it’s adequately supported by the underlying ground. In fact, Gunsaullus stated that of the 150-plus projects she works on annually with MBA, pressure grouting is only used about once a year. Unless there is a known problem such as a leak or visible bottom settlement, owners can typically save their money and skip the pressure grouting.
Myth #2: Perimeter Roof Handrails Are Mandated
Many tank owners, in an effort to comply with OSHA standards, will add handrails along the entire perimeter of the roof. But this expensive proposition usually isn’t necessary. OSHA clarified as much by issuing an interpretation of Standard 1910.23: Guarding Floor and Wall Openings and Holes. The Standard Interpretation states that the top of a tank may be a “roof” or a “platform,” depending on the amount of traffic it gets. Pursuant to that designation, handrails would not be required on a “roof.”
That said, safety should always be a priority. AWWA tank standards recommend handrails and steps or a platform for steep slopes, and partial handrails around risky work areas are also a wise investment. All of these improvements, however, can be done at the owner’s discretion.
Myth #3: Overcoating Is Always Economical
As part of regular maintenance, it is possible to “overcoat,” or to apply a new layer of paint over the old one(s). This is fine practice, given that overcoating can add 10 to 20 years to a system and save a lot of money — when conditions for application are right. But some tank inspectors/contractors always recommend this because it’s in their best interest, but not necessarily the tank owner’s.
A myriad of factors must be considered before overcoating, including the age, type, adhesion properties, and thickness of the new coating, as well as how many times the tank has been overcoated. If the accumulation gets too thick and heavy, the coatings will peel off prematurely.
If conditions aren’t right for overcoating, all paint must be removed and the surface properly prepped for the new coating. Though this is a more difficult task (which is likely the reason contractors often opt for overcoating), doing it right the first time is the better and more cost-effective alternative to replacing the coating in two or three years because of peeling.
Myth #4: OSHA Upgrades Are Grandfathered In
Gunsaullus shared the story of confronting a tank owner about an exterior ladder that was obviously out of compliance with OSHA standards. According to Standard 1910.27: Fixed Ladders, the width of the ladder must be at least 16 inches, the rungs no more than 12 inches apart (and uniformly spaced), and the ladder at least 7 inches away from the tank (to allow proper room for boots to climb). The ladder on this particular tank failed on all these fronts, but the owner felt no compunction to comply with OSHA regulations because he thought the 40-year-old tank was “grandfathered in.”
That Gunsaullus listed this misperception as a top myth suggests that it is somewhat common. It can also be expensive — even deadly. The repercussions for not keeping up with OSHA standards include fines, accidents, and litigation. Gunsaullus counsels tank owners to be vigilant with regard to awareness and handling of their mandated safety responsibilities. “The bottom line is it’s just the right thing to do,” she said.
Myth #5: AWWA Upgrades Are Required Immediately
In another story from the field, a consultant performing a safety and security audit at a treatment plant recommended that a ladder be added on the interior of a tank to comply with AWWA standards. Conveniently, the consultant also provided installation services. The ladder was attached while the tank was in service, with underwater welding utilized in the process. When MBA performed an inspection a few years later, the ladder was only partially affixed, with portions of it seemingly missing — portions that were soon discovered at the bottom of the tank.
The above picture shows the broken-down ladder at the bottom of the tank, just eight years after installation.
This was another situation that could have ended with a serious injury, but it’s one that could have been avoided altogether by not installing the ladder — especially while the tank was in use, which can impede proper installation. Unlike OSHA standards, AWWA standards are not mandatory; they simply represent sound design considerations. “It’s a really good guide to improve the operation of your tank and extend its lifespan,” said Gunsaullus of AWWA’s tank standards, “but you don’t have to do it.”
In a scenario like the one detailed above, the AWWA (and consultant’s) recommendation should have been at the very least delayed, if not rejected. Gunsaullus advises tank owners that non-mandated upgrades should only be considered truly necessary when they address a clear safety hazard or will extend the life of the tank. Instead of striving for immediacy, upgrades should be suspended, when possible, until the tank is out of service. Exceptions would include, again, a safety situation, or when an opening or hole in the tank could permit animals or debris to get in.
As an addendum to these five now-debunked myths, Gunsaullus suggested that an anniversary inspection on any new or rehabbed tank be conducted a year later, just to be sure the job is holding up as it should. A well-cared-for tank can last in excess of 100 years, but unnecessary work based on bad information will cost you excess money. Here’s hoping these tips help save your tank and your budget.
Do these pointers ring true for you, based on your experience with tank repair? Are there any further “myths” or best practices you can provide? Share your thoughts below…