Corrosion Issues = Planning Issues

By Paul Brake, P.Eng., Dynamic Machine Design
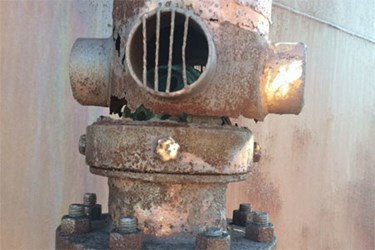
Corrosion Is the Fruit of Poor Planning
Corrosion & Erosion, Hand in Hand
There indeed is a desperate need for a corrosion science. We have all seen perfect, shiny new equipment quickly rot and deteriorate in the field. Put a new motor in a pulp mill and two years later you cannot even read the label on it. String in a new stainless steel spool and a little while later you have pinhole leaks at the welds. To the right you see a fire suppression foam changer on an API 650 storage tank. It is only a few years old, but out in the wind and weather, next to the ocean, it has rotted completely away. Imagine if there was a tank fire. Do you thing that foam chamber would be effective?
In many industrial processes there is a requirement for metallurgical engineers to investigate, research and develop solutions for safe handling of chemicals. In larger industrial settings there is also a need for the assistance of corrosion specialists when integrating numerous pieces of varying equipment into a process. For example if you are transporting hydrofluoric acid at 300 Celsius through a pressurized pipe, you get an expert to tell you how. For many process situations we do have regulatory bodies and industry standard associations to help us. ASME, API, NFPA, etc. are perfect examples.
Outside of the Extreme
There is however another facet of the corrosion game. Many corrosion issues we face daily in industry have extremely simple solutions. Most are caused by an abject failure to educate ourselves before making decisions. All that is required is a little reading. There are untold resources, free and available at your fingertips if you have Internet and can type. There are some basic consideration that can save you a fortune and a lot of pain downstream.
Common Galvanic Corrosion
First is the problem of dissimilar metals. In general this is a BAD thing. When you are forced to use contacting dissimilar metals the first thing to note is the relative nobility of the metals. The further apart that number is, the fast one of them is going to rot away. This is further exacerbated by the amount of water present, and the amount of electrolytes in that water, and the temperature. For example, you have warm municipal wastewater with a low pH, full of various salts as it always is, traveling through a carbon steel pipe; if you need to divert that wastewater with a hose and decide to use an aluminum cam lock fitting (yes, I have seen that done on more than one occasion), that decision will come back to haunt you in a few weeks. I know of another example in an oil refinery where they decided to use a titanium tube bundle in a heat exchanger. The feed pipe to the exchanger was 18 inches in diameter, to give you an idea of the scale we are talking about. The shell was about six feet in diameter and about 30 feet long. They did everything right except electrically isolating the dissimilar metals. The shell of the exchanger and the pipes feeding it were carbon steel. It was not long before they had to replace the shell and ten feet of pipe on either side.
The Process Side of Things
The next notable consideration is the chemical compatibility of your materials to your process flow. There are many tables online to help. And always, and I mean always, consult chemical compatibility tables when choosing materials for piping, fittings, tanks, vessels etc. For example, did you know that ketchup will eat through PVC piping? I didn’t either until I consulted a chemical compatibility table. What goes with what, and what doesn’t are not always intuitive. Similarly, many people mistaking think that stainless steel is stainless. It is simply corrosion resistant, under certain conditions. The rejects from a reverse osmosis desalination system will eat through 316 SS. You would need at the very least a 2205 duplex, or preferably a 2507 super-duplex.
Operating Conditions
Then you must consider the temperature and temperature variation. And it is not just for the acceptable temperature range of the material, you must also consider the coefficient of thermal expansion, and the relative thermal expansion coefficients when dealing with differing materials. Laminations can peal off with heating and cooling. Piping can buckle, fitting can be snapped off. I have seen it happen. And it is not just a one time thing, it might last for a couple of months, but with each temperature cycle you get fatigue building up. Then one day, on a long weekend, you get called in to clean up because a fitting broke and nobody can figure out why.
What Else?
There is also the issue of coatings. There are many corrosion resistant coatings available for different applications. Here I definitely suggest calling the experts. And supplier of coatings should have in-house experts that will recommend the best coatings for your application if you give them accurate details up front. There are also more advanced solutions like Cathodic and Impressed Current Protection. They may seem like black magic to some, but they can work wonderfully. For example, when we replace the floor on one of our crude storage tanks, we also include a Cathodic Protection and liner. This literally adds years to the life of the tank.
Then there are things like Stress Corrosion Cracking, Corrosion Under Insulation (CUI) and Hydrogen Embrittlement, and my favorite, Microbiologically Induced Corrosion (MIC). In reality, for these you might want to consult and expert.
So for basic corrosion issues, please consult the many free and available documents that can make your life, and the life of your operators and maintainers much easier. They will thank you for it. Well, maybe not but they should. And for those funky situations where the process contains odd chemicals, high pressures etc, consult an expert and save everyone a lot of grief. Remember most corrosion issues are just the fruit of planning errors.