An Unconventional Approach To Dairy Wastewater Treatment
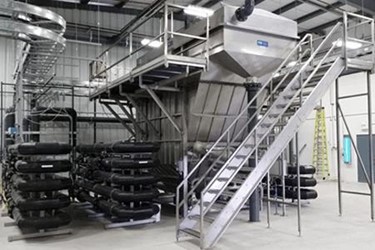
If you’ve ever looked into the ice cream freezers at your local grocery store you can imagine all the different ingredients you’d find at the ice cream factory: cream, sugar, chocolate, fruit, nuts, milk, syrups, and so on. With a little effort, you might also imagine that when washing out all the equipment used to make ice cream, some of these ingredients are washed down the drain. In reality, the volume of wastewater generated at an industrial ice cream factory can be pretty significant, which means that there is a lot to clean up before sending that water out to the city sewer system.
For those acquainted with wastewater management you are familiar with the process of pretreatment. For strangers to the field, pretreatment is the first stage of mechanical or chemical interventions used to remove contaminants in wastewater like oil, grease, and particulates. Industrial facilities that produce significant volumes of wastewater (>5,000 GPD) are required by law to pretreat their wastewater to a specified quality before they are allowed to send it into the sewer. The penalty for not meeting these standards can be severe — to the tune of tens of thousands of dollars a month, or in some cases result in forcible plant closure until the problem is fixed. Needless to say, most industrial facilities install and operate on-site wastewater pretreatment systems. Those who don’t, generally contract to have the water hauled away to some other facility for treatment.
The case of our ice cream plant is an interesting one because the design of the pretreatment system could have gone in two different directions. The split became apparent when deciding which chemical process should be used to remove the oil and solids in the wastewater. Some advocated one path, while we were resolved on another. Here’s a little bit about the two options.
The Conventional Approach
In most industrial pretreatment applications where solids removal is the main objective, the chemical prescription is fairly straightforward — neutralize pH with acid or caustic soda, coagulate solids with a metal salt, and then agglomerate solids into larger chunks using a polymer flocculant so they float or sink. Then a dissolved air flotation (DAF) system removes solids from the water. This process is depicted in Figure 1 below.
Figure 1. Conventional Pretreatment Process Diagram
The success of the conventional chemical approach in any wastewater stream is highly dependent on flow rate and composition consistency, but especially so in dairy applications. As wastewater discharges are inconsistent in volume and interval, the general approach is to incorporate an equalization (EQ) tank into the design (as detailed in Figure 1). The EQ tank is sized to hold approximately 4 to 8 hours of flow, catching and mixing it to normalize wastewater composition. This allows the treatment equipment to be calibrated to a relatively consistent contaminant load at a steady flow rate. However, using a large EQ tank in dairy effluents becomes problematic as milk products quickly spoil and release foul odors. Of course, odor control mechanisms can be implemented (i.e., buried tanks, tank covers, air scrubbers), but not without significant capital and operational costs.
Odor is one problem, but even more difficult to handle is the volatility of the dairy wastewater as it is stored for hours on end. In milk, various microorganisms alter the chemical environment over time and as temperature fluctuates. Through this process sugars are converted into lactic acid, proteins are converted into ammonia, and pH values go down and up. The unstable nature of milk in dairy plant effluents makes the correct chemical dosing rates a moving target, which, from an operations perspective, is both challenging and expensive. What’s more, it makes the final water quality a bit of a guessing game. That is a difficult situation when the threats of heavy fines and plant shutdowns are looming.
The rate at which dairy products ferment in the wastewater treatment process is also troublesome on the backend of the DAF system. Skimmed sludge in its semi-solid form degrades even faster than the liquid wastewater, which generates obnoxious odors and a stinking solid mass of unusable material. The use of metal salts in the coagulation process make the float sludge unfit for rendering or any other practical use. The sludge literally becomes a secondary waste product.
The conventional process is satisfactory from an overall treatment perspective, but all the downsides make it a less-than-ideal solution.
The Acidulation Process
The alternative approach to treating the ice cream plant wastewater involves a different chemical process — acidulation. In the acidulation process, sulfuric acid is used to lower wastewater pH to the level where the emulsified oils and milk proteins coagulate which is between 3.9 and 4.3. After coagulation, a flocculant is dosed to amass the coagulated particles together. Both of these chemical treatments are applied in small chemical reaction vessels, called pipe flocculators. Solids separation still occurs in a DAF system, with final pH neutralization occurring in a third flocculator as seen in Figure 2.
Figure 2. Acidulation Process Diagram
The acidulation process directly addresses the concerns associated with the conventional chemical approach. Large equalization tanks are unnecessary because there’s no need to blend the wastewater to a consistent pollutant composition. Instead, all water receives the same chemical treatment to lower pH. This is all done automatically, with inline pH sensors and acid dosing pumps doing the heavy lifting. Operators don’t have to guess and modify coagulant dosing on the fly because there is no coagulant.
There is no nuisance odor as the acidic environment inhibits the fermentation process. This makes starting up and shutting down the equipment a simple matter, as there’s no need to worry about stagnant water releasing obnoxious odors.
An added benefit of the acidulation process is the overall reduction in generated sludge volume. Using a metal-based salt, like aluminum sulfate or ferric chloride, can add significantly to the amount of secondary waste produced in the treatment process. Acidulating the water allows the proteins to coagulate without additional bulky chemicals. This minor change can reduce sludge production by tens of thousands of pounds a week, resulting in big savings on sludge hauling and disposal.
Which Process Was Selected?
Despite the clear upsides to the acidulation process, there was real opposition from some other parties to implementing an unconventional approach with so much time and capital on the line. Some said that it simply wouldn’t work, others said that it was too risky. Despite the resistance we knew it would work and strongly advised that acidulation was the way to go.
In the end, our recommendation won out and the acidulation process was implemented with great success. Operations are consistent and automatic, there are no odor problems, and wastewater pretreatment requirements are met. Ultimately, the acidulation design approach reduced project and operations costs by 15 to 20 percent, which will amount to millions of dollars over the life of the system. Not bad for a system that some professed just wouldn’t work.
About FRC Systems International:
FRC Systems International designs and builds wastewater treatment systems for organizations across all industry sectors, including dairy products manufacturers. With over 500 installations in more than 20 countries, FRC has established a reputation as a trusted wastewater solutions provider. Learn more at www.frcsystems.com or follow FRC Systems on LinkedIn.