Wastewater Plant To Turn Grease And Food Scraps Into Energy
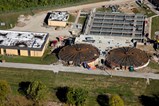
The City of West Lafayette, Indiana has nearly completed a major renovation project at its wastewater treatment plant (WWTP) that will allow the city to convert fats, oils, and grease (called FOG) and food scrap waste from Purdue University to produce energy that will be used to help operate the plant. This innovative waste-to-energy treatment system will reduce the plant's overall operating and maintenance costs, decrease the overall carbon footprint of the community, and reduce waste going to landfills.
Kennedy/Jenks Consultants, as an engineering sub-consultant to M.D. Wessler & Associates, designed innovative digester upgrades to replace two 50-year-old anaerobic digesters with a new, efficient, externally-pumped mixing system housed inside a new digester building. The building also incorporates a new sludge heating system, with heat exchangers and a boiler, and a co-generation system that will use the digester gas (methane) to generate electricity and heat.
Converting Waste to Energy
"Our renovations allow us to capture the methane gas produced at the plant and use it to produce electricity through two new microturbines," says Dave Henderson, Utility Director for the City of West Lafayette, Indiana. "To augment methane production, we also have a new fats, oils, and grease (FOG) receiving station that allows us to introduce waste grease from restaurants into the digester to boost our methane production. The methane gas will generate between 20 to 30% of the total electricity needed to operate the plant processes. An added plus is that grease haulers will pay tipping fees for dumping their grease, and this will generate revenue for the plant and help pay for the costs of our renovation."
An exciting outgrowth of the original project is the chance to use food waste as a potential energy source. "We just completed a 3-week pilot project with Purdue University," relates Henderson. "We took food waste from the university's dining courts and added that to the digesters through the central grease-receiving station. The university was already separating out the food waste from other waste for a composting project. Although the composting project ended, they were still separating the food from other waste. It was a perfect opportunity to take this preprocessed pulp matter and use it in the digesters to increase energy production. There was only minimal added expense to make this work.
"We were very pleased with the initial results," added Henderson. "We worked out the logistics of receiving this new source and the digesters responded very well to the food waste. We're excited about this potential new waste stream going into the digesters. The normal digestion process produces 37 cu. ft. of gas per minute. Adding FOG doubles the amount of digester gas. By adding the food waste from Purdue, the plant could get 10% more energy. Purdue can avoid paying fees for disposing of the food waste at the landfill while we will get the benefit of converting that food waste to energy.
"Although the use of food waste improved gas production, the additional cost to allow the plant to treat the food waste was minimal," adds Henderson. "We bought a portable cart lifter to tip the digested food waste into the grease-receiving station. The university is just across the street from the plant, so the cost of transporting the waste was far less than for hauling it to the landfill. Both the city and university staffs are excited about this project and are pleased with the results so far. Although we still have a few details to work out, the chances of implementing this plan are very good. I think we will be taking food waste from the university this fall."
"The city is hoping to eventually expand the food waste program to commercial facilities such as the local Wal-Mart and food markets," says Henderson. "We are also considering accepting glycerine which is a by-product of the bio-diesel refinement process. The waste from a local refiner is currently being sent to the landfill. By using this process, we could significantly reduce the waste going to landfills and produce additional digester gas."
Another sustainable feature also grew out the original project. "We added a couple of vehicle charging stations at the plant," states Henderson. "The City plans to purchase electric vehicles to use at the plant and we will be able to charge them overnight using energy produced by the microturbines at the plant."
Ribbon Cutting Expected Soon
Construction of the plant upgrades is nearly completed, and the ribbon-cutting ceremony is expected in late June or early July.
"This is a much more effective use of our existing digester capacity," says Henderson. "The city was thinking of adding another digester, but the Kennedy/Jenks study and design showed that was unnecessary. They showed us that we could just use our existing capacity and add other fuel sources to produce our own electricity. This process has increased the longevity of our process with a minimum of cost. This project has saved costs, maximized our resources, minimized additional structures, and increased the sustainability of our plant."
Kennedy/Jenks Consultants has provided engineering and scientific solutions for municipal agencies and industries since 1919 and celebrates its 90th anniversary this year. The employee-owned firm has 25 offices serving clients nationwide –providing consulting services to the water environment, transportation, federal, and industrial sectors.
SOURCE: Kennedy/Jenks